Worldwide Used Consumer Die Casting. For the business of manufacturing bulk orders of parts made from non ferrous metals such as tin, zinc, copper or the most popular of them all, aluminum. Aluminum has become very popular in Consumer Parts …
Continue reading
Category Archives: Auto Parts
Zinc Die Cast Knobs
Zinc die-cast knobs are essential components in various industries, offering durability, versatility, and aesthetic appeal. With excellent strength and corrosion resistance properties, zinc die-cast knobs have become a popular choice for manufacturers due to their ability to withstand both indoor and outdoor applications. This article will delve deeper into the characteristics, benefits, applications, and considerations of zinc die-cast knobs in the manufacturing sector.
Zinc die-cast knobs are manufactured through a process called die casting, which involves injecting molten zinc into a steel mold cavity under high pressure. This process allows for the production of intricate and precise designs, making zinc die-cast knobs a versatile option for various applications. The use of zinc as a base material also contributes to the knobs’ strength and resistance to wear and tear, ensuring a long lifespan even in demanding environments.
One of the key advantages of zinc die-cast knobs is their aesthetic appeal. The material can be easily plated or coated with various finishes, including chrome, nickel, or powder coating, to match different design requirements. This versatility in finishing options allows manufacturers to tailor the appearance of zinc die-cast knobs to suit a wide range of products, from industrial machinery to consumer electronics.
In addition to their visual appeal, zinc die-cast knobs offer excellent tactile feedback and ergonomic functionality. The knobs can be designed with different shapes, sizes, and textures to provide users with a comfortable grip and precise control. This makes zinc die-cast knobs ideal for applications where precise adjustment or manipulation is required, such as in instrumentation panels, control systems, or consumer appliances.
Another significant benefit of zinc die-cast knobs is their cost-effectiveness. The die-casting process allows for high production volumes at a relatively low cost per unit, making zinc die-cast knobs a cost-efficient solution for manufacturers looking to scale up their production. Furthermore, the durability and longevity of zinc die-cast knobs reduce maintenance and replacement costs, providing long-term value for businesses.
Zinc die-cast knobs find wide applications across various industries, including automotive, electronics, furniture, and machinery. In the automotive sector, zinc die-cast knobs are used in dashboard controls, door handles, and HVAC systems, providing drivers with reliable and durable components. In the electronics industry, zinc die-cast knobs are commonly found in audio equipment, home appliances, and industrial machinery, where precision and durability are paramount. When considering zinc die-cast knobs for a specific application, manufacturers should take into account factors such as operating environment, load requirements, and aesthetic considerations. It is essential to work closely with experienced design engineers and material specialists to ensure that the chosen zinc die-cast knobs meet the desired performance criteria and quality standards.
“The Parts We Make Today, We Ship Today”
Kinetic Die Casting Company. Inc.
6918 Beck Avenue, North Hollywood,
California 91605, United States of America
E-mail sales@kineticdc.com
USA Toll Free: (800) 524-8083 Local: (818) 982-9200
To get prices for Die Casting Tooling Molds or Parts:
RFQ Die Casting Tooling Part Prices
Kinetic Die Casting Company makes:
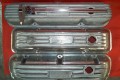
Die Casting Bracket Hardware
Airplane Die Casting Parts
Permalink: https://www.kineticdiecasting.com/kdc/zinc-die-cast-knobs/
Revolutionizing Automotive Engineering
Aluminum Car Part Die Castings are used where efficiency, performance, and safety are important, the choice of materials and manufacturing processes plays a critical role in shaping the future of vehicle design. Among the myriad manufacturing techniques available, aluminum die casting stands out as a game-changer, offering unparalleled versatility, strength, and efficiency in producing car parts. From engine components to structural elements, aluminum die castings have revolutionized automotive engineering, driving innovation and excellence in vehicle manufacturing. Let’s delve into the significance of aluminum car part die castings and explore their transformative impact on the automotive industry.
Aluminum die casting enables the production of automotive parts with intricate geometries, tight tolerances, and complex features that would be challenging or cost-prohibitive to achieve using traditional manufacturing methods. Through advanced die casting techniques such as high-pressure die casting (HPDC) and vacuum die casting, automotive engineers can create components with superior dimensional accuracy, surface finish, and mechanical properties. This precision engineering translates into enhanced performance, reliability, and durability of vehicle systems, contributing to a smoother, more responsive driving experience for consumers.
As the automotive industry continues to prioritize sustainability and environmental responsibility, aluminum die casting emerges as a preferred manufacturing solution due to its eco-friendly properties. Aluminum is highly recyclable, with the ability to be melted down and reused indefinitely without compromising its mechanical properties. By incorporating recycled aluminum into die casting processes, automakers can reduce energy consumption, greenhouse gas emissions, and raw material extraction, contributing to a more sustainable and circular economy.
Aluminum car part die castings have revolutionized automotive engineering, offering a winning combination of lightweight design, precision engineering, durability, and sustainability. As automakers continue to innovate and push the boundaries of vehicle design and performance, aluminum die casting will remain a cornerstone technology, driving progress and excellence in the automotive industry. From fuel-efficient engines to sleek body designs, aluminum die castings are shaping the future of mobility, delivering vehicles that are safer, more efficient, and more environmentally friendly.
“The Parts We Make Today, We Ship Today”
Kinetic Die Casting Company. Inc.
6918 Beck Avenue, North Hollywood,
California 91605, United States of America
E-mail sales@kineticdc.com
USA Toll Free: (800) 524-8083 Local: (818) 982-9200
To get prices for Die Casting Car Parts:
Quote Prices for Die Casting Car Parts/font>
Kinetic Die Casting Company makes:
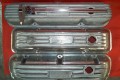
Die Casting Bracket Hardware
Airplane Die Casting Parts
Manufacturing Excellence in California
The State of California USA, renowned for its innovation, diversity, and entrepreneurial spirit, stands as a beacon of manufacturing excellence within the United States. From cutting-edge technology and aerospace advancements to sustainable practices and artisanal craftsmanship, the state’s manufacturing sector encompasses a broad spectrum of industries, each contributing to its vibrant and dynamic economy. Let’s explore the multifaceted landscape of manufacturing in California and the factors that have propelled its growth and success. Manufacturing Excellence: The Dynamic Landscape of Manufacturing in California
California’s manufacturing sector spans a diverse array of industries, reflecting the state’s rich tapestry of innovation and creativity. From Silicon Valley’s high-tech giants and biotech innovators to Southern California’s aerospace pioneers and Central Valley’s agricultural powerhouses, California is home to a multitude of manufacturing hubs driving progress and prosperity across the state and beyond. Whether it’s advanced electronics, sustainable energy solutions, precision machinery, or artisanal goods, California’s manufacturing prowess knows no bounds.
Innovation and Technology Leadership, at the forefront of innovation and technology, California’s manufacturing sector continually pushes the boundaries of what’s possible. Silicon Valley, situated in the San Francisco Bay Area, serves as the epicenter of technological innovation, driving advancements in semiconductors, software development, and digital manufacturing. With a concentration of world-class research institutions, venture capital firms, and entrepreneurial talent, California remains a global leader in fostering innovation and nurturing startups that are revolutionizing the manufacturing landscape.
Aerospace and Defense Manufacturing Excellence, Southern California boasts a rich heritage in aerospace and defense manufacturing, with iconic companies such as Boeing, Lockheed Martin, and Northrop Grumman calling the region home. From designing and manufacturing cutting-edge aircraft and spacecraft to developing advanced defense systems and components, California’s aerospace industry continues to push the boundaries of aerospace engineering and innovation. With a skilled workforce, robust supply chain, and close collaboration with government agencies and research institutions, California remains a vital hub for aerospace manufacturing excellence.
Sustainability and Green Manufacturing, California leads the nation in embracing sustainable manufacturing practices and green technologies aimed at reducing environmental impact and promoting sustainability. From renewable energy solutions and zero-emission vehicles to eco-friendly packaging and waste reduction initiatives, manufacturers across the state are pioneering innovative approaches to mitigate climate change and create a more sustainable future. With stringent environmental regulations and a commitment to corporate social responsibility, California’s manufacturing sector serves as a global model for sustainable and responsible production practices.
Skilled Workforce and Education Initiatives, California’s manufacturing success is underpinned by its highly skilled and diverse workforce, supported by a robust network of educational institutions, vocational training programs, and workforce development initiatives. From community colleges and technical schools to apprenticeship programs and industry partnerships, California invests in preparing the next generation of manufacturing talent, ensuring a steady pipeline of skilled workers equipped to meet the evolving needs of the industry. Additionally, initiatives promoting diversity, equity, and inclusion are fostering a more inclusive and equitable manufacturing workforce reflective of California’s diverse population.
Global Connectivity and Trade, As a global economic powerhouse, California benefits from its strategic location and robust trade connections, serving as a gateway to international markets. With world-class ports, airports, and logistics infrastructure, California facilitates the movement of goods and services to and from key markets around the world. International trade agreements and partnerships further enhance California’s position as a global manufacturing hub, facilitating the exchange of ideas, technologies, and resources that drive innovation and economic growth. Manufacturing in California is characterized by innovation, diversity, and a relentless pursuit of excellence. From technological breakthroughs and aerospace advancements to sustainability initiatives and workforce development, California’s manufacturing sector continues to shape the future of industry and drive economic prosperity both within the state and beyond. As innovation and collaboration thrive, California remains at the forefront of manufacturing innovation, paving the way for a brighter, more sustainable future.
“The Parts We Make Today, We Ship Today”
Kinetic Die Casting Company. Inc.
6918 Beck Avenue, North Hollywood,
California 91605, United States of America
E-mail sales@kineticdc.com
USA Toll Free: (800) 524-8083 Local: (818) 982-9200
To get prices for Die Casting Tooling Molds or Parts:
RFQ Die Casting Tooling Part Prices
Kinetic Die Casting Company makes:
Die Casting Business
Die Casting Manufacturing
Die Casting Driving Innovation
Die Casting Revolutionizes Car Parts Manufacturing, where performance, efficiency, and safety are paramount, the quality and precision of every component can make all the difference. Enter die casting, a manufacturing process that has revolutionized the production of car parts, offering unmatched precision, versatility, and efficiency. From engine components to structural elements, transmission housings to suspension components, die casting plays a pivotal role in shaping the future of automotive engineering. Let’s explore how die casting has transformed the manufacturing landscape of car parts and its profound impact on the automotive industry.
Strength and Lightweight Design. In the pursuit of fuel efficiency and performance, automotive engineers are constantly seeking ways to reduce vehicle weight without compromising strength and durability. Die casting provides an ideal solution, allowing manufacturers to produce lightweight parts with exceptional structural integrity. Aluminum and magnesium alloys, commonly used in die casting, offer a winning combination of strength and weight savings, making them well-suited for automotive applications. By leveraging die casting techniques, car manufacturers can design and fabricate components that enhance fuel efficiency, increase payload capacity, and improve overall performance.
The engine serves as the heart of any vehicle, relying on a multitude of precision-engineered components to deliver power efficiently and reliably. From cylinder heads and engine blocks to intake manifolds and transmission cases, die casting plays a critical role in the production of these vital parts. By utilizing die casting processes, automotive manufacturers can achieve the tight tolerances and intricate geometries required for optimal engine performance. Moreover, die casting enables the production of complex shapes and features that would be difficult or impossible to achieve using traditional machining methods, further enhancing engine efficiency and reliability.
Safety is a top priority in automotive design, and vehicle structures must withstand the forces encountered during normal operation and in the event of a collision. Die casting enables the production of parts with uniform grain structure and minimal porosity, resulting in enhanced mechanical properties and crashworthiness. Whether it’s chassis components, suspension parts, or body reinforcements, die-cast parts contribute to the overall strength and safety of vehicles, ensuring passenger protection and structural integrity.
The transmission and drivetrain systems are critical to the performance and efficiency of vehicles, requiring precision-engineered components to transfer power smoothly and reliably. Die casting is instrumental in the production of transmission housings, differential cases, and gearbox components, providing the strength, dimensional accuracy, and heat dissipation capabilities necessary for optimal performance. By leveraging die casting techniques, automotive manufacturers can achieve the intricate geometries and complex features required for advanced transmission systems, improving overall drivability and fuel efficiency.
As automotive technology continues to evolve, so too does the role of die casting in shaping the future of vehicle manufacturing. Manufacturers and engineers collaborate to push the boundaries of innovation, leveraging advanced materials, design optimization techniques, and cutting-edge manufacturing processes to meet the evolving needs of the automotive industry. From lightweight structural components to high-performance engine parts, die casting remains at the forefront of automotive innovation, driving progress and shaping the next generation of vehicles.
Die casting has revolutionized the manufacturing of car parts, offering automotive manufacturers the precision, efficiency, and reliability required to meet the demanding standards of the industry. From enhancing fuel efficiency to improving vehicle safety, die-cast parts play a vital role in shaping the future of automotive engineering, ensuring that vehicles continue to drive innovation and performance on the road ahead.
Permalink: https://www.kineticdiecasting.com/kdc/die-casting-driving-innovation/
“The Parts We Make Today, We Ship Today”
Kinetic Die Casting Company. Inc.
6918 Beck Avenue, North Hollywood,
California 91605, United States of America
E-mail sales@kineticdc.com
USA Toll Free: (800) 524-8083 Local: (818) 982-9200
To get prices for Die Casting Car Parts:
Quote Car Parts Die Casting Prices
Kinetic Die Casting Company makes:
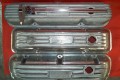
Die Casting Bracket Hardware
Airplane Die Casting Parts
The Versatility of Aluminum and Sand Casting Parts in Modern Manufacturing
The Versatility of Aluminum and Sand Casting Parts in Modern Manufacturing
In the realm of modern manufacturing, the utilization of aluminum and sand casting parts has become integral to the production of a wide array of products across various industries. The versatility, durability, and cost-effectiveness of aluminum, combined with the flexibility and intricacy of sand casting processes, have made this combination a go-to choice for many manufacturers looking to create high-quality components.
**Aluminum: The Material of Choice**
Aluminum stands out as a favored material for manufacturing due to its exceptional properties. Its lightweight nature, excellent corrosion resistance, high strength-to-weight ratio, and ability to be easily machined make it an ideal choice for a multitude of applications. From automotive parts to aerospace components, aluminum’s versatility knows no bounds.
One of the key advantages of aluminum is its ability to be recycled repeatedly without losing its inherent properties. This sustainability factor not only reduces manufacturing costs but also aligns with the growing emphasis on environmentally friendly practices in the industry.
**Sand Casting: A Time-Tested Technique**
Sand casting, one of the oldest known metal casting processes, complements the properties of aluminum perfectly. This versatile technique involves using a mold made of compacted sand to shape molten metal into a desired form. The flexibility of sand casting allows for the production of complex geometries and intricate designs, making it ideal for creating unique components that often cannot be achieved through other manufacturing methods.
The process of sand casting offers several advantages, including cost-effectiveness, suitability for both small and large production runs, and the ability to quickly create prototypes for testing and validation. Its adaptability to a wide range of alloys, including aluminum, further enhances its appeal in modern manufacturing.
**The Synergy of Aluminum and Sand Casting Parts**
The combination of aluminum and sand casting parts unlocks a realm of possibilities for manufacturers seeking high-quality, bespoke components. Aluminum’s exceptional properties, such as its strength, corrosion resistance, and thermal conductivity, make it an excellent choice for a diverse range of applications, including automotive, aerospace, marine, and industrial sectors.
By harnessing the intricacies of sand casting, manufacturers can achieve precision and detail in their aluminum parts, ensuring that each component meets the exact specifications required for optimal performance. The ability to produce components with thin walls, complex shapes, and tight tolerances underscores the synergy between aluminum and sand casting in delivering top-tier products.
Furthermore, the cost-effectiveness and efficiency of the aluminum and sand casting combination make it a preferred choice for manufacturers looking to streamline their production processes while maintaining high standards of quality.
**In Conclusion**
In the landscape of modern manufacturing, the union of aluminum and sand casting parts stands as a testament to innovation, quality, and efficiency. The remarkable properties of aluminum, coupled with the flexibility and precision of sand casting processes, create a harmonious synergy that enables the production of superior components across a multitude of industries. As technology advances and demands for intricate and reliable components grow, the role of aluminum and sand casting in shaping the future of manufacturing remains pivotal.
“The Parts We Make Today, We Ship Today”
Kinetic Die Casting Company. Inc.
6918 Beck Avenue, North Hollywood,
California 91605, United States of America
E-mail sales@kineticdc.com
USA Toll Free: (800) 524-8083 Local: (818) 982-9200
To get price quotes for Die Casting Tooling Molds or Die Casting Parts:
Quote Die Casting Prices
Kinetic Die Casting Company makes:
Automotive Die Casting Parts
Die Casting Bracket Hardware
Airplane Die Casting Parts