What is Die Casting Porosity? In order for you to know what die casting porosity is, you need to know the basics. Die casting is a process wherein a particular amount of molten metal is put inside a container, then …
Continue reading
Category Archives: Die Casting Parts
Sand Casting Compared to Die Casting
Sand Casting Compared to Die Casting. If you are wondering which is better- sand casting or die casting – then this is the right article for you. Whether you need to know about sand casting or die casting advantages or a assessment of both, this article will certainly help you.
In order to have a stronger view of what is better, you must first know what these two methods are all about. Sand casting, as its name proposes, forms its mold with the help of a pattern or model which is pressed into a kind of sand mixture. Die casting on the other hand utilizes toughened tool steel as a mold in making its cast parts.
Both processes are decent choices of metal casting method. It just determined by what kind of metal parts you plan to cast or produce. For big hollow metal parts like cast aluminum automobile parts, sand casting is characteristically used. For minor and more detailed metal parts, die casting is the more perfect process. The casting weight range for sand casting is essentially unlimited while die casting has a range from 1oz up to 20 pounds.
When it comes to mass producing parts, which involves intricate details and flat surface, die casting is the more ideal method. It is because die casting process has a dimensional tolerance of as low as .001 inch, while sand casting has a minimum of .010 inches.
Money-wise, initial expenses for die casting are pricier than the first costs used for of sand casting. Nevertheless, in the long run, die casting has a lot inexpensive labor cost associated to the labor cost experienced by sand casting.
Like
Kinetic Die Casting Company on FaceBook

This is the blog on the Kinetic Die Casting Company web site. We are an Aluminum Die Casting Company. Look at this website page for more details: www.kineticdiecasting.com/aluminum_die_casting.html. Contact Kinetic Die Casting Company at 818-982-9200 or email us at sales@kineticdc.com. Use this webpage to request “die casting part prices” www.kineticdiecasting.com/replyform.html
@kineticdc #kineticdc
Metal Die Cast in the Cold Chamber
Metal Die Cast in the Cold Chamber. In the field of metallurgy, the cold chamber method is known as one of the two chief types of die casting processes. The other one is called the hot chamber method. If you noticed sculpted metal parts with a high melting point, they are in all probability fashioned by a cold chamber machine. Cold chamber die castings could be created out of aluminum, magnesium die casting, and copper.
These cold chamber die castings go through outside furnaces. The metals are then poured into a cold chamber in the machine. The cylinder and plunger are not submerged in liquefied metal as is the method with low melting point metal alloys in a hot chamber method. These enormous machines use hydraulic power to force the poured metal into the die mold. It is a slower procedure but the machines utilized for cold chamber die castings usually last longer. This and its capability to manufacture metals with a high melting point into exactitude parts make it helpful for machinists, metallurgists, metalworkers, engineers, and manufacturers of our modern gadgets like aluminum die cast boxes that are utilized in electrical outlets and other such electrical fixtures.
Die casting is only one of the procedures utilized to shape metal to our wants. There is also forging, rolling, sintering, machining, fabrication, metalworking, and numerous other different casting procedures. Then there are the practices of fusing one metal to another which are soldering, welding, and brazing. There are also other procedures such as annealing, tempering, quenching, plating, thermal spraying, and case hardening. All these metalworking methods have given to the development of our world as we know it today.
Kinetic Die Casting makes great quality aluminum, and Zinc Die Casting If looking for a job or would like a quote please visit our website:Kinetic Die Casting Company
Die Casting Part Prices
Kinetic Die Casting Company discusses how Die Casting Part Prices are determined. A die casting company is sometimes also known as a Job Shop Manufacturer. In other words, the die casting company provides metal products to other manufacturing companies. These other manufacturing companies, sometimes are OEMs (Original Equipment Manufacturers). These die casting metal products, die castings, are used in the product produced by the OEM customer, who is always a manufacturing company.
Die casting part prices or diecastings prices are determined using only a few factors.
- Utilities Costs (Water, Gas and Electric)
- Overhead and Fixed Costs
- The Cost of Labor Rates
- The Number of Labor Hours
- Setup Costs for equipment and die casting molds
- Die Casting Metal Amounts
- Die Casting Metal Cost Each Pound
- Value Added Processes.
All of these variables listed to manufacture die casting parts. Typically die castings cost less than $1.00 to $5.00 each die casting part.
- Utilities Costs – Are used to melt the die casting metal for two or four hours prior to die casting production. The high pressure die casting machines use a lot of electricity to operate the high pressure pumps.
- Overhead and Fixed Costs – These are costs that are frequently overlooked, such as Rent, Insurance, Medical Benefits and Salaries for Management and Owners.
- The Cost of Labor Rates – There are typically many different labor rates depending on the job an employee does or the work experience and time in service.
- The Number of Labor Hours – Labor hours are the hours the die casting machine made parts but sometimes may include hours in inspection, packaging and processing.
- Setup Costs for equipment and die casting molds – There are hours of setup required before a die casting machine can make parts. It takes a few hours to put a die into the die casting machine, it takes a few hours to mount inserts into a mold base, it takes a few hours to melt a bath of metal before production begins.
- Die Casting Metal Amounts – How much die casting metal does each part need? How much was used to produce the part? How much needs to be removed in the clean up process? How much metal was lost and how much can be recovered?
- Die Casting Metal Cost Each Pound – Various die casting metal alloys have a different cost each pound. Some alloys are common and cost less than the more uncommon alloys. If an alloy is used for only one job, there is sometimes a minimum metal lot cost for the bath.
- Value added processes also sometimes known as Outside Process costs – The processes that are required to change the casting from the raw state to a completed part that our customer wants has a cost. Machining costs and coating costs are the more typical value added costs.
These costs are spread through out the production run of hundreds or thousands of diecast parts. When our customer needs only a few parts, they will need to pay a higher cost each die casting part to cover some of the variable and minimum costs.
Another Web Page with Die Casting Part Cost Information:
https://www.kineticdiecasting.com/kdc/optimal-die-casting-production-part-quantity/
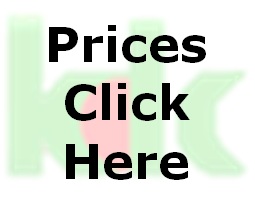
Die Casting Part Prices
Contact Kinetic Die Casting Company to get a die casting part cost or die casting part prices:
Kinetic Die Casting Company
6918 Beck Avenue
North Hollywood, California USA
818-982-9200
sales@kineticdc.com