08/10/2023 – For nearly 30 years, Kinetic Die Casting Company has been a small manufacturing company located in the Los Angeles, California area. We make aluminum die casting parts and zinc die casting parts for our manufacturing customers. We are …
Continue reading
Category Archives: Diecasting Process
Die Casting Part Prices
Kinetic Die Casting Company discusses how Die Casting Part Prices are determined. A die casting company is sometimes also known as a Job Shop Manufacturer. In other words, the die casting company provides metal products to other manufacturing companies. These other manufacturing companies, sometimes are OEMs (Original Equipment Manufacturers). These die casting metal products, die castings, are used in the product produced by the OEM customer, who is always a manufacturing company.
Die casting part prices or diecastings prices are determined using only a few factors.
- Utilities Costs (Water, Gas and Electric)
- Overhead and Fixed Costs
- The Cost of Labor Rates
- The Number of Labor Hours
- Setup Costs for equipment and die casting molds
- Die Casting Metal Amounts
- Die Casting Metal Cost Each Pound
- Value Added Processes.
All of these variables listed to manufacture die casting parts. Typically die castings cost less than $1.00 to $5.00 each die casting part.
- Utilities Costs – Are used to melt the die casting metal for two or four hours prior to die casting production. The high pressure die casting machines use a lot of electricity to operate the high pressure pumps.
- Overhead and Fixed Costs – These are costs that are frequently overlooked, such as Rent, Insurance, Medical Benefits and Salaries for Management and Owners.
- The Cost of Labor Rates – There are typically many different labor rates depending on the job an employee does or the work experience and time in service.
- The Number of Labor Hours – Labor hours are the hours the die casting machine made parts but sometimes may include hours in inspection, packaging and processing.
- Setup Costs for equipment and die casting molds – There are hours of setup required before a die casting machine can make parts. It takes a few hours to put a die into the die casting machine, it takes a few hours to mount inserts into a mold base, it takes a few hours to melt a bath of metal before production begins.
- Die Casting Metal Amounts – How much die casting metal does each part need? How much was used to produce the part? How much needs to be removed in the clean up process? How much metal was lost and how much can be recovered?
- Die Casting Metal Cost Each Pound – Various die casting metal alloys have a different cost each pound. Some alloys are common and cost less than the more uncommon alloys. If an alloy is used for only one job, there is sometimes a minimum metal lot cost for the bath.
- Value added processes also sometimes known as Outside Process costs – The processes that are required to change the casting from the raw state to a completed part that our customer wants has a cost. Machining costs and coating costs are the more typical value added costs.
These costs are spread through out the production run of hundreds or thousands of diecast parts. When our customer needs only a few parts, they will need to pay a higher cost each die casting part to cover some of the variable and minimum costs.
Another Web Page with Die Casting Part Cost Information:
https://www.kineticdiecasting.com/kdc/optimal-die-casting-production-part-quantity/
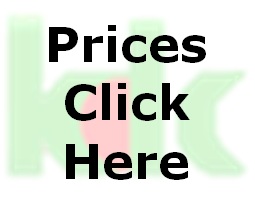
Die Casting Part Prices
Contact Kinetic Die Casting Company to get a die casting part cost or die casting part prices:
Kinetic Die Casting Company
6918 Beck Avenue
North Hollywood, California USA
818-982-9200
sales@kineticdc.com
Die Casting
Die Casting is a metal parts manufacturing process in which molten metal alloy is injected with pressure into a heat treated and hardened steel mold or die casting die. Metal parts are produced at the rate of one part or part cycle every minute. The typical ten hour day will yield 600 or more metal die castings.
Take a look at our web pages for more information:
1. What Is Die Casting?
(http://www.kineticdiecasting.com/what-is-die-casting.html)
2. Why Use Die Castings?
(http://www.kineticdiecasting.com/why-use-diecasting.html)
3. Die Casting Limitations?
(http://www.kineticdiecasting.com/capabilities.html)
4. Die Casting Videos
(http://www.youtube.com/user/kineticdc)
Get Traffic To Your Product
This Die Casting Blog (https://www.kineticdiecasting.com/kdc/) gets over 500 visitors daily. Do you want to get 500 people looking at your product? Daily? Send me you article with the links you need to your product, and I will post it on this blog. Send your article to sales@kineticdc.com
Kinetic Die Casting Company 6918 Beck Avenue North Hollywood California USA 91605
Draft Angles in Die Castings
Kinetic Die Casting Company discusses “Draft Angle in Die Castings” – “what is draft angle in an aluminum metal box casting?” or “why do I need a draft angle on my aluminum die casting box part?” The mechanical reply is, all aluminum die castings need a draft angle on the walls of die cast box parts perpendicular to the parting plane or parallel to the slide interfaces. Because I have been selling die cast parts for over 20 years, I find easy answers and give simple calculations for my clients. What does that have to do with the usual engineer (any engineer other than in tooling or mechanical) or professional buyer?
Most people do not have the need to worry about how things are made; only what is made, and will it be what is essential. “Have you ever observed on a cupcake the bottom diameter is smaller than the top diameter?” or “Have you noted that a cake pan has sides that slope in toward the middle of the pan?” That would be an extreme case of a draft angle. Aluminum die castings would stick inside the die casting tool, molds, or die casting die if there was not enough draft angle in the tool and part. The usual draft angle for an aluminum die casting part is two degrees per side. The calculation for that is easy if a anyone is acquainted with die casting production part design.
Imagine an enclosure (or Aluminum Box) lying on a counter with the open side up. The aluminum box is 2″ deep inside with the height and width 4″ each way on outside. The walls of the box are 0.10″ in width. Due to the wall’s thickness, a few things are obvious to a part designer regarding this seemingly simple box:
A 2 degree draft angle will alter the dimensions in the following on the interior and exterior and should be regarded if something needs to fit inside the box or outside the box:
If the box was intended for the interior of 4″ x 4″ at the bottom: box:
See our die casting draft webpage: http://www.kineticdiecasting.com/draft.html
Contact Kinetic Die Casting Company at 800-524-8083 for more information
http://www.youtube.com/user/kineticdc
March 1 A360 Metal Flow Video
Auto Parts Manufactured as Die Castings in A360 Aluminum Die Casting Alloy.
The Metal Flow Video from Kinetic Die Casting Company
Published on Mar 1, 2013 on:
http://www.youtube.com/watch?v=P2hJylJ8Qrc
Kinetic Die Casting Company, 818-982-9200. A die casting Metal Flow Video into a four cavity die casting mold making four die casting automotive parts. Molten metal, A360 Aluminum alloy is injecting into the die casting mold. This video is a simulation of checking for die casting part surface defects and the metal temperature of the metal flow. Die Casting A360 Aluminum Alloy Metal Flow Video into an a360 aluminum auto part.
Kinetic Die Casting Videos
(http://www.youtube.com/user/kineticdc)
Contact us by calling us at 818-982-9200 and ask for sales or email us at sales@kineticdc.com. Visit our website at www.kineticdiecasting.com
Doug Taylor of Delmar Die Casting Remembered
Doug Taylor passed away January 11, 2013. I will miss Doug Taylor. I have known Doug Taylor since April 2005, when he invited me to the Governor’s Ball at the NADCA annual event in St. Louis, Mo. Even knowing my die casting company was much smaller than his, he always treated me with respect. I never understood why, but he seemed to like me even if we were competitors. We talked many times and had lunch many times. Once during lunch, he asked that I sell my tiny die casting company and go to work for him as his president. He offered me a lot of money and a car. We laughed when I explained that I am unemployable.
In September 2008, Doug called me to visit him for lunch and he offered to sell me Del Mar Die Casting Company. He offered the zinc die casting business and the magnesium die casting business from Del Mar Industries. We met together over the next few months to see how we could make it work out. During the due diligence I got to meet his team and his family. Everyone at Delmar was excellent, just like Doug. Doug was very patient with me and my team. We came very close to closing the sale but we could not get the deal closed. Doug continued to be friendly afterwards. He was a gentleman in every sense of the word.
– Bob Thomas, President
Kinetic Die Casting, Inc.
This excerpt is from NADCA:
Longtime NADCA member Doug Taylor passed away on January 11, 2013. Doug was a tremendous NADCA member and supporter. He always said that he found the warmest and most generous people in the die casting industry, and he had never met such great friends.
Doug joined the team at Del Mar Die Casting in 1981 and became president and CEO in January of 1986. Under Doug’s leadership, Del Mar Die Casting acquired Gardena Planting and Los Angeles Die Casting, becoming Del Mar Industries. Doug received the Austin T. Lillegren Award in 2010, which is presented in recognition of loyal and extraordinary services to the association and the die casting industry.
A strong supporter of NADCA, Doug attended every Executive Conference from 1989-2010, and every NADCA Government Affairs Briefing from 1987-2010 until his retirement in 2010. During his terms on NADCA’s Board, he only missed one meeting out of 52. Doug joined the Board in 1992 as one of the original 28 Board members of the newly formed NADCA, serving a total of 13 years on the Board.
The service for Doug Taylor will be held at 11:00 AM on Friday, January 25th at the following address:
Westwood United Methodist Church
10497 Wilshire Blvd.
Los Angeles, CA 90024
Doug and all of his great stories will be missed.