For many years car parts have been made from aluminum. For the last few decades car parts have been made from aluminum diecastings. Car parts that are made of aluminum diecastings are: Valve Covers, Aluminum Alloy Wheels, Carburetors and specialty …
Continue reading
Category Archives: Diecasting Process
What is the Difference between “Low Pressure” and “High Pressure” Die Casting Parts in 2023?
High Pressure Die Casting Parts. What is the difference between “Low Pressure” and “High Pressure” Die Casting Parts?
Kinetic Die Casting Company makes high pressure die casting parts. The term “Die Casting”, in the USA means a high pressure process whereas in Europe it means a low pressure manufacturing process.
High Pressure Aluminum Die Casting? High pressure die casting is a manufacturing process in which molten metal (aluminum) is injected with a die casting machine under force using considerable pressure into a steel mold or die to form products. …. READ MORE: High Pressure Die Casting
High Pressure Die Casting Machine
High Pressure Die Casting Machine
Low pressure die casting is similar to sand casting. Gravity is used fill the molten metal into the mold. This process is much slower, about five minutes or more per part (less than 100 parts per day) than high pressure die casting (more than 500 parts per day), about a part every minute. The part cost for high pressure die casting is much less than low pressure die casting.
Kinetic Die Casting is a Los Angeles die casting company that manufactures aluminum and zinc parts. If you would like more information, please visit our website:Kinetic Die Casting Company
“The Parts We Make Today, We Ship Today”
Kinetic Die Casting Company. Inc.
6918 Beck Avenue, North Hollywood,
California 91605, United States of America
E-mail sales@kineticdc.com
USA Toll Free: (800) 524-8083 Local: (818) 982-9200
To get prices for Die Casting Tooling Molds or Parts:
RFQ Die Casting Tooling Part Prices
Kinetic Die Casting Company makes:
Die Casting Manufactured using Lean Manufacturing in 2023
Lean Manufacturing Die Casting. Die Casting Parts Manufactured using Lean Manufacturing.
Everyone believes the die casting is solely a “Batch & Que” manufacturing process. Most die casting companies operate using a the department layout (example.
- Die Casting Department – 500 Parts produced day one (1) shipped to the trim department on day two (2).
- Trimming Department – 500 Parts get trimmed on day two (2) and get shipped to machining department on day three (3).
- Machining Department – 500 Parts get machined in machining department on day three (3) and sent to quality department on day four (4).
- Quality Department – 500 Parts get inspected on day four (4) and sent to shipping department on day five (5).
- Shipping Department – 500 Parts are packaged on day five (5) and shipped to customer on day six (6).
- 500 Parts are shipped at least six days after initial production in the die casting machine.
500 parts produced on the first day of the week get shipped (6)six days later, typically next week. If there is a one (1) day Que in each department, it will add another four (4) days to the six (6) days making the delivery ten (10) days after production.
6 – 10 additional days is a long time to wait for die casting parts for some customers.
The Kinetic Die Casting Company Difference –
What if a die casting company changed from the department layout and went to lean manufacturing production cell layout?
- Die casting one (1) part in one (1) minute is sent to trimmer. Continues making one (1) part a minute until 500 parts complete in 500 minutes or 8.33 hours.
- Trimmer trims (1) part 1/4 (.25) minutes and sends (1) part to machine area. Continues trimming next 499 parts.
- Machine taps three holes in one (1) part 1/4 (.25) minutes and sends one (1) part for inspection. Continues machining 499 parts.
- Inspector checks one (1) part for 1/4 (.25) minutes and sends one (1) part to shipping. Continues inspecting 499 parts.
- Shipper packs one (1) part in box 1/8 (.12) minutes. Continues packing 499 parts.
- 500 parts complete and shipped to customer in less than ten (10) hours, one shift.
Kinetic Die Casting Company uses a lean die casting manufacturing process to produce die casting parts for our customers. At Kinetic Die Casting Company, in 99% of the 500 part or less production orders, we ship them today.
Get Die Casting Part Prices from us today:
http://www.kineticdiecasting.com/replyform.html
Kinetic Die Casting manufactures die cast parts for their customers. If you would like to know more about what is die casting or if you would like a quote, please visit our website:Kinetic Die Casting Company
“The Parts We Make Today, We Ship Today”
Kinetic Die Casting Company. Inc.
6918 Beck Avenue, North Hollywood,
California 91605, United States of America
E-mail sales@kineticdc.com
USA Toll Free: (800) 524-8083 Local: (818) 982-9200
To get prices for Die Casting Tooling Molds or Parts:
RFQ Die Casting Tooling Part Prices
Kinetic Die Casting Company makes:
Die Cast Manager Job
Kinetic Die Casting Company, Inc. has a position available for a Die Casting Manager Job. This person will supervise production processes, housekeeping, enforce our safety policies and plant rules for the Die Cast department. Job duties may include supervising or personally setting controls, operating or training use of die casting machines, maintaining production equipment, troubleshooting, and repairing the die casting machines, furnace and other related equipment in the Die Cast Department.
Five 5 years or more of aluminum die cast or plastic mold injection molding experience preferred. We prefer experience as a Die Casting Machine Operator, Die Cast Setup Man, Leadman or Foreman. You must have at least a minimum of two years of experience working in a die-casting company or plastic injection molding company. Forklift experience is a plus. Pay or Salary is negotiable, based on experience.
Use our online Die Casting Job Application
https://www.kineticdiecasting.com/application.php
Come by or Email or Mail your job resume and salary or pay requirements to:
Kinetic Die Casting Company, Inc.
6918 Beck Avenue
North Hollywood, California 91605
Sales@kineticdc.com 818-982-9200
#DieCastingJobs https://www.kineticdiecasting.com/employment.html
#Job #Jobs #employment #diecasting #diecast #manager #supervisor
Aluminum Heatsinks: What They Do 2023
Aluminum Heatsink
Aluminum heat sinks expels heat from parts and components in electronic applications. Aluminum die cast heatsinks are designed in a way that needs less machining than other manufacturing processes. The cooling fins can be manufactured at the same time as the mounting holes. Heatsink parts are made with all features necessary for cooling electronic components and to mount the heat sinks on the printed circuit board (PC board). Aluminum heat sinks have a high dimensional stability. Heat sink production begins as soon as the die casting tooling is produced. Aluminum heat sinks are produced at the rate of 250 heat sink parts per day to 2,500 heat sink parts per day. Heatsinks look good as raw parts or can be anodized or powdercoated.
Pictures of Heatsink Die Casting Parts
To get a price for aluminum die casting parts or die casting tooling, call toll free 800-524-8083 and ask for sales. Or email us at sales@kineticdc.com for a fast response on a price quote.

Kinetic Die Casting Company 6918 Beck Avenue, North Hollywood, California 91605, United States of America
E-mail sales@kineticdc.com USA Toll Free: (800) 524-8083 Local: (818) 982-9200
To get prices for Die Casting Tooling Molds or Parts: RFQ Die Casting Part Prices
Kinetic Die Casting Company makes:
Automotive Die Casting Parts
Die Casting Bracket Hardware
Airplane Die Casting Parts
Zinc Die Casting Company California
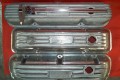