Prototype Parts and Die Casting Parts. We can help you develop your metal product with prototype parts. Kinetic Die Casting Company can make prototype metal parts for our customers, to use for evaluation, prior to making die casting tooling. We …
Continue reading
Category Archives: newsletter
Limitations of Kinetic Die Casting Company
#KineticDC makes parts for American #Manufacturing Companies ( #diecasting ). Kinetic Die Casting Company (www.kineticdc.com) supports manufacturing companies all over the USA, in California, where we are located, or Arizona and Texas and as far away as Ohio, Connecticut, South Carolina and New York. We make metal parts in various die casting alloys.
Aluminum Die Casting Alloys (98% of our business)
A360 aluminum (Mostly used for Automotive and Lighting including low copper A360)
A380 aluminum (Most common alloy) Including A383 and A384
A413 aluminum (Mostly used in Aircraft, Heat sinks and Lighting)
Zinc Die Casting Alloys – Cold Chamber (2% of our business)
#3 Zinc (ZAMAK 3) Most common zinc die casting alloy.
#5 Zinc (ZAMAK 5)
Die Casting Part Sizes and Die Casting Part Weights we have made:
Smallest part we have made is 0.25 inches by 0.25 inches for BK Lighting Company weighing a few grams
Largest part we have made is 17 inches by 14 inches for Pioneer Roofing Tile Company weighing 8 pounds.
Die Casting Production Quantity:
Lowest quantity of parts shipped to Parker-Hannifin Corp. FSD of ten (10) parts on purchase order.
Highest quantity of parts shipped for pump housings of over 250,000 parts in a year.
Production Parts Delivery:
Purchase Order (PO) receipt to production shipment in less than 4 weeks.
Expedite to less than a week is possible.
Transfer tool to KDC for production in 4 weeks or less is typical.
New Tooling Delivery:
New die casting tooling from China supplier in about 8 weeks for part samples.
New tooling from USA supplier in about 12 weeks for part samples.
Right now is a good time to contact us for production die casting parts.
Kinetic Die Casting Company (www.kineticdc.com) 6918 Beck Avenue, North Hollywood, California 91605
Phone: 818-982-9200 ——- Email: sales@kineticdc.com
KDC Closed Labor Day 2015
Kinetic Die Casting Company will be closed on Monday September 7, 2015 in observance of Labor Day.
Some fun facts from the US Department of Labor about Labor Day History:
The first Labor Day holiday was celebrated on Tuesday, September 5, 1882, in New York City, in accordance with the plans of the Central Labor Union. The Central Labor Union held its second Labor Day holiday just a year later, on September 5, 1883.
In 1884 the first Monday in September was selected as the holiday, as originally proposed, and the Central Labor Union urged similar organizations in other cities to follow the example of New York and celebrate a “workingmen’s holiday” on that date. The idea spread with the growth of labor organizations, and in 1885 Labor Day was celebrated in many industrial centers of the country.
Permalink: https://www.kineticdiecasting.com/kdc/kdc-closed-labor-day-2015/
Blue Light Special on Airport Lights
How Kinetic Die Casting Company helped a Airport Lighting Parts Manufacturer. To get help for your company, use this webpage: Prices for Die Casting Parts. George had an idea on how he could develop a better airport runway lighting product. In the 1990s, Kinetic Die Casting Company received a fax from a company called Airport Lighting Company. At Airport Lighting Company, George, makes the lighting products of many of the airports in America. One of his biggest product lines is the blue light on the side of runways. The product in use is a round steel plate that is machined with mounting holes that are drilled and counter bored. The center was a larger hole that is then drilled and threaded for an arm that stands about a foot tall holding a lamp light fixture with a blue light bulb. These steel round plates line the side of runways for airplanes.
George at Airport Lighting Company has a problem regarding his blue lamp runway light fixtures. Steel rusts. The steel plates he uses for the runway lights rust in bad weather, which causes the plate to collapse if a plane runs over the plate by accident. Aluminum die casting does not rust. Will an aluminum die casting plate be strong enough to hold the weight of an airplane?
George contacted Kinetic Die Casting Company with the question, how strong is aluminum die casting? Our engineer, Dante, created a solidworks model of an aluminum plate with strengthening ribs and gussets. We tested the model using software to test the strength. We sent George the test results and he was ecstatic. He commissioned us to build his tool and has purchased thousands of the aluminum plates. George created his own Blue Light Special on Airport Runway Lights.
Look out of the airplane window the next time you fly, those blue lights may be sitting on an aluminum plate that just may have been made by Kinetic Die Casting Company.
Contact us to help you develop your aluminum product for die casting design. sales@kineticdc.com
#manufacturing #diecasting #kineticdc
Light Fixture Die Casting Parts
Kinetic Die Casting Company makes aluminum die castings as Lighting Fixture Die Castings. We make these parts every day and ship thousands of these aluminum die castings every week.
Contact us to get die casting prices http://www.kineticdiecasting.com/replyform.html.
Kinetic Die Casting Company
6918 Beck Avenue
North Hollywood, California 91605
Sales@kineticdc.com
Thank You For Transferring Tools To KDC
This was an exciting week at Kinetic Die Casting Company. We were notified that two customers that they were sending us die casting tools. One tool is a 12 x 15 unit tool that makes an aircraft part and the second tool is a complete mold with a trim die that makes a lighting product.
We are still offering a Tooling Transfer special.
These manufacturing companies customer transferred their die casting tooling
Kinetic Die Casting Company, a better die casting part supplier.
Kinetic Die Casting Company makes that decision easier.
1. Send us your die casting tooling and die casting molds
2. A purchase order made to us with your old suppliers prices.
3. We will honor the die casting part price paid to the old die casting part supplier.
4. You will get better die casting parts than you received before.
5. We will ship the die casting parts to you in less than 4 weeks.
Kinetic Die Casting Company 6918 Beck Avenue North Hollywood California 91605 USA
Office Hours: Monday through Thursday 6:00 AM to 4:30 PM (Pacific Time)
818-982-9200 – sales@kineticdc.com – www.kineticdiecasting.com
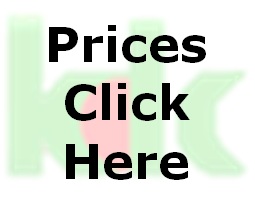
Die Casting Part Prices
“The Parts We Make Today, We Ship Today”
Kineticdc makes:
Automotive Die Casting Parts
Airplane Die Casting Parts
Light Fixture Die Casting Parts
Consumer Products Aluminum Parts
Aerospace Die Casting Parts
Military Die Casting Parts
Die Casting Manufacturing in California
Kinetic Die Casting Company manufactures die casting parts in North Hollywood California. We posted earlier this year about our California Manufacturing Technology Consulting® (CMTC) listing as a California Manufacturing Company.
There are a lot of details available on the CMTC website Made in California – Kinetic Die Casting Company
Kinetic Die Casting Company makes aluminum die casting parts for manufacturing companies. Since 1994, we have made parts for many manufacturing industries such as Aerospace, Military, Commercial, Lighting , Automotive and Consumer Products. The Parts We Make Today, We Ship Today. Our niche is lower quantity (less than 500 parts) production orders, delivered quickly. We ship parts typically in less than four weeks. Some of our customers send us blanket purchase orders of several thousands of parts to be delivered over a twelve week period. We can supply 1 die casting part or 500,000 die casting parts in a year to you.
Quick Facts:
SIC 3363 Aluminum Die Casting Company
NAICS 331512 Aluminum Die Casting Company
SBA Small Disadvantaged Die Casting Business
Minority Owned Die Casting Business (Native American)
Veteran Owned Die Casting Business
Processes:
Lean manufacturing of die casting production.
Aluminum die casting parts up to 8 pounds.
Zinc die casting parts up to 5 pounds.
Die casting tooling, molds and dies.
Die casting trim dies.
Machining die casting parts.
Assembly of die casting components.
Paint or powder coating.
Plating, burnishing and polishing.
CONTACT KDC TODAY:
Kinetic Die Casting Company, Inc.
Location: North Hollywood, CA
Phone: 818-982-9200
Email: sales@kineticdc.com
Website: www.kineticdiecasting.com