Functions of a Die Casting Company. Die casting is an ordinary procedure in the metalworking industry. Die cast metal parts are being utilized by a lot of companies around the world. Almost all contemporary products that we utilize daily have …
Continue reading
Die Casting Porosity and Its Causes in 2023
Die Casting Porosity and Its Causes. Die Casting porosity is one of the most common defects in the die casting manufacturing industry. What is die casting porosity? Die Casting porosity is a kind of die casting factory imperfection in which the die cast parts have tiny spaces which covers air within the metal – henceforth, the die cast parts become porous. The porosity of die casting parts could weaken the parts itself if the spaces or voids are very big.
To clearly understand the causes of the porosity one must know the basic of the die casting procedure. In a nutshell, die casting procedure includes molding molten metal by placing it inside a short cylinder, and then a great force is applied by a piston connected on the cylinder, pushing the molten metal so it would take the form of the die cast die or die cast mold. During this process, the metal is forced along with the air inside of the cylinder to the die casting mold.
Die casting porosity could be added by several factors like the following:
•
Die casting machine pressures.
•
Temperature of the metal and the mold.
•
The cleanliness of the materials used.
•
Design of the die casting mold.
•
Design of the die casting part.
•
The shot speed of the die casting machine utilized.
•
Die casting mold release or die casting spray
Die casting manufacturers use metals that are non-ferrous or metals that don’t have iron. It is because iron content is the chief reason for oxidation and rusting. Non-ferrous metals include magnesium, tin, lead, copper, zinc and aluminum.
This is the blog on the Kinetic Die Casting Company web site. Here are some Die Casting Parts Pictures Images. Look at this website page for more details: www.kineticdiecasting.com/kdcgallery/index.php. Contact Kinetic Die Casting Company at 818-982-9200 or email us at sales@kineticdc.com. Use this webpage to request “die casting part prices” www.kineticdiecasting.com/replyform.html
“The Parts We Make Today, We Ship Today”
Kinetic Die Casting Company. Inc.
6918 Beck Avenue, North Hollywood,
California 91605, United States of America
E-mail sales@kineticdc.com
USA Toll Free: (800) 524-8083 Local: (818) 982-9200
To get prices for Die Casting Tooling Molds or Parts:
RFQ Die Casting Tooling Part Prices
Kinetic Die Casting Company makes:
Optimal Die Casting Production part Quantity in 2023?
Optimal Die Casting Production Part Quantity? “I need to buy several thousands of parts to buy die castings”. That is the most common myth or false belief people have regarding the optimal die casting part production quantity. We believe, the optimum production quantity of die casting parts is, the quantity of parts you need to buy.
Unfortunately, many die casting companies also believe the “high quantity only” myth. Some die casting companies perpetuate that myth to force their customers into buying more parts than they need. They refuse smaller quantity purchase orders unless their customers pay a very high “set-up charge”. Sometimes, they will push out delivery of lower part quantities to over 12 weeks, in an effort to dissuade the lower quantity part purchase orders. Then sometimes the part quality is “lacking” but the parts are needed so badly, the sub-quality parts are accepted because we do not have 12 more weeks to wait for replacement parts.
Kinetic Die Casting is thrilled to accept die casting part purchase orders of any quantity. We will accept part purchase orders with deliveries of 10,000 parts or less. Many of our part purchase orders have part deliveries of less than 1,000 parts. In fact, many of our aerospace part purchase orders have deliveries of less than 100 parts and sometimes less than 10 parts.
Our part deliveries range from four to six (4-6) weeks for raw castings. No matter what quantity you want, as long as it is less than 10,000 parts. In most cases we will ship your parts in less than six weeks, if we do not need to wait for outside processes to hold up our part delivery.
In most production part purchase orders, we ship your parts the day we make your parts. We do not have departmental delays that can take several days or weeks to process the parts after the parts are produced.
Our optimal die casting part production quantity, is the quantity you want to buy. Contact us today for a competitive price. Your delivery will be less than six weeks.
Kinetic Die Casting Company
818-982-9200
sales@kineticdc.com
“The Parts We Make Today, We Ship Today”
Kinetic Die Casting Company. Inc.
6918 Beck Avenue, North Hollywood,
California 91605, United States of America
E-mail sales@kineticdc.com
USA Toll Free: (800) 524-8083 Local: (818) 982-9200
To get prices for Die Casting Tooling Molds or Parts:
RFQ Die Casting Tooling Part Prices
Kinetic Die Casting Company makes:
Extruded Aluminum Heatsinks in 2023
Extruded aluminum heatsinks are made by heating aluminum to the point of a semi-solid state. Then this aluminum is pushed (extruded) through an extrusion die. These aluminum forms have the profile of the die it was pushed through, much like the play dough toy extruder. The simple shapes are stars or circles. These forms are cut to the length needed.
Aluminum Heatsinks that are extruded typically have a flat bottom and ribs on the top. They can be extruded in lengths of several feet an cut to shorter lengths. Because these extruded aluminum heatsinks were formed by pushing through a die, there is a limitation on details that can be formed on the top and bottom surfaces. If a depression is needed to mount components then it will need to be machined into the part as a pocket as an after operation, dramatically increasing the part cost. More typically, if holes are needed for mounting, they too will need to be machined into the parts as a secondary operation. Any other holes needed so wires or components can pass through have the same limitation.
The Aluminum Die Casting Process injects metal into a mold or die that forms the top, bottom and sides. Mounting holes, through holes and cavity indentations formed into the part are in the die halfs on the top and bottom. Aluminum Die Casting Heatsinks will have all the features necessary for installing the components and the holes for mounting during the original manufacturing operation. Die casting heatsinks will not require secondary operations for holes and features.
Kinetic Die Casting manufactures aluminum and zinc die casting parts. Samples of KDC’s work include die cast speaker parts, aluminum tile plates, and other die cast metal parts. If you would like to have a quote please visit our website: Kinetic Die Casting Company
Kinetic Die Casting Company 6918 Beck Avenue, North Hollywood, California 91605, United States of America
E-mail sales@kineticdc.com USA Toll Free: (800) 524-8083 Local: (818) 982-9200
To get prices for Die Casting Tooling Molds or Parts: RFQ Die Casting Part Prices
Kinetic Die Casting Company makes:
Automotive Die Casting Parts
Die Casting Bracket Hardware
Airplane Die Casting Parts
Zinc Die Casting Company California
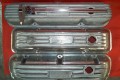
General Die Casters and Dart Die Casting Merge
NADCA – North American Die Casting Association reports that Dart Die Casting Company and General Die Casters Company Merge. General Die Casters, Inc. (Twinsburg, OH) is joining forces with Dart Casting, Inc. (Alsip, IL) under common ownership. The new organization will operate 41 casting machines between 400 and 1200 ton and 28 CNC machining centers, creating one of the leading middle-market die cast companies in the Midwest with the ability to leverage each company’s capabilities and customer base to continue a trajectory of growth.
Each company’s management teams will remain in place and key contacts will remain the same. Both teams are excited to combine their talents and become one of the most capable and cost competitive high pressure die casting companies in the country.