Die casting parts and the alloys used to make them. When undergoing die casting, the type of metal alloy used determines the specific type of die casting that should be employed and the quality by which the die casting parts …
Continue reading
Optimal Die Casting Production part Quantity in 2023?
Optimal Die Casting Production Part Quantity? “I need to buy several thousands of parts to buy die castings”. That is the most common myth or false belief people have regarding the optimal die casting part production quantity. We believe, the optimum production quantity of die casting parts is, the quantity of parts you need to buy.
Unfortunately, many die casting companies also believe the “high quantity only” myth. Some die casting companies perpetuate that myth to force their customers into buying more parts than they need. They refuse smaller quantity purchase orders unless their customers pay a very high “set-up charge”. Sometimes, they will push out delivery of lower part quantities to over 12 weeks, in an effort to dissuade the lower quantity part purchase orders. Then sometimes the part quality is “lacking” but the parts are needed so badly, the sub-quality parts are accepted because we do not have 12 more weeks to wait for replacement parts.
Kinetic Die Casting is thrilled to accept die casting part purchase orders of any quantity. We will accept part purchase orders with deliveries of 10,000 parts or less. Many of our part purchase orders have part deliveries of less than 1,000 parts. In fact, many of our aerospace part purchase orders have deliveries of less than 100 parts and sometimes less than 10 parts.
Our part deliveries range from four to six (4-6) weeks for raw castings. No matter what quantity you want, as long as it is less than 10,000 parts. In most cases we will ship your parts in less than six weeks, if we do not need to wait for outside processes to hold up our part delivery.
In most production part purchase orders, we ship your parts the day we make your parts. We do not have departmental delays that can take several days or weeks to process the parts after the parts are produced.
Our optimal die casting part production quantity, is the quantity you want to buy. Contact us today for a competitive price. Your delivery will be less than six weeks.
Kinetic Die Casting Company
818-982-9200
sales@kineticdc.com
“The Parts We Make Today, We Ship Today”
Kinetic Die Casting Company. Inc.
6918 Beck Avenue, North Hollywood,
California 91605, United States of America
E-mail sales@kineticdc.com
USA Toll Free: (800) 524-8083 Local: (818) 982-9200
To get prices for Die Casting Tooling Molds or Parts:
RFQ Die Casting Tooling Part Prices
Kinetic Die Casting Company makes:
Extruded Aluminum Heatsinks in 2023
Extruded aluminum heatsinks are made by heating aluminum to the point of a semi-solid state. Then this aluminum is pushed (extruded) through an extrusion die. These aluminum forms have the profile of the die it was pushed through, much like the play dough toy extruder. The simple shapes are stars or circles. These forms are cut to the length needed.
Aluminum Heatsinks that are extruded typically have a flat bottom and ribs on the top. They can be extruded in lengths of several feet an cut to shorter lengths. Because these extruded aluminum heatsinks were formed by pushing through a die, there is a limitation on details that can be formed on the top and bottom surfaces. If a depression is needed to mount components then it will need to be machined into the part as a pocket as an after operation, dramatically increasing the part cost. More typically, if holes are needed for mounting, they too will need to be machined into the parts as a secondary operation. Any other holes needed so wires or components can pass through have the same limitation.
The Aluminum Die Casting Process injects metal into a mold or die that forms the top, bottom and sides. Mounting holes, through holes and cavity indentations formed into the part are in the die halfs on the top and bottom. Aluminum Die Casting Heatsinks will have all the features necessary for installing the components and the holes for mounting during the original manufacturing operation. Die casting heatsinks will not require secondary operations for holes and features.
Kinetic Die Casting manufactures aluminum and zinc die casting parts. Samples of KDC’s work include die cast speaker parts, aluminum tile plates, and other die cast metal parts. If you would like to have a quote please visit our website: Kinetic Die Casting Company
Kinetic Die Casting Company 6918 Beck Avenue, North Hollywood, California 91605, United States of America
E-mail sales@kineticdc.com USA Toll Free: (800) 524-8083 Local: (818) 982-9200
To get prices for Die Casting Tooling Molds or Parts: RFQ Die Casting Part Prices
Kinetic Die Casting Company makes:
Automotive Die Casting Parts
Die Casting Bracket Hardware
Airplane Die Casting Parts
Zinc Die Casting Company California
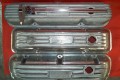
General Die Casters and Dart Die Casting Merge
NADCA – North American Die Casting Association reports that Dart Die Casting Company and General Die Casters Company Merge. General Die Casters, Inc. (Twinsburg, OH) is joining forces with Dart Casting, Inc. (Alsip, IL) under common ownership. The new organization will operate 41 casting machines between 400 and 1200 ton and 28 CNC machining centers, creating one of the leading middle-market die cast companies in the Midwest with the ability to leverage each company’s capabilities and customer base to continue a trajectory of growth.
Each company’s management teams will remain in place and key contacts will remain the same. Both teams are excited to combine their talents and become one of the most capable and cost competitive high pressure die casting companies in the country.
NADCA in 2023
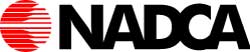
Kinetic Die Casting Company is a member of the North American Die Casting Association NADCA. We have been corporate members for a very long time. The North American Die Casting Association (NADCA) is the sole trade and technical association of the die casting industry. NADCA membership consists of both corporate and individual members from over 950 companies located in every geographic region of the U.S.
These companies include custom die casters (who produce die castings for sale to others), captive die casters (who produce castings for their own use in manufacturing a product), and suppliers to the die casting industry. NADCA members can be found in every type of community across the nation, representing both rural and urban interests.
The North American Die Casting Association (NADCA) represents the voice of the die casting industry. NADCA is committed to promoting industry awareness, domestic growth in the global marketplace and member exposure. Headquartered in Wheeling, IL, the association is comprised of both individual members and corporate members located throughout United States, Canada and Mexico.
The North American Die Casting Association (NADCA) also has an extensive government relations program based in Washington D.C. The program provides government affairs services to NADCA members. NADCA relies on the services of Waterman & Associates to act as the ears, eyes and voice of the die casting industry at the federal level.

“The Parts We Make Today, We Ship Today”
Kinetic Die Casting Company. Inc.
6918 Beck Avenue, North Hollywood,
California 91605, United States of America
E-mail sales@kineticdc.com
USA Toll Free: (800) 524-8083 Local: (818) 982-9200
To get prices for Die Casting Tooling Molds or Parts:
RFQ Die Casting Tooling Part Prices
Kinetic Die Casting Company makes:
Sponsored Listings:
House in Florida
What is the Aluminum Die Casting Process?
Aluminum die casting is a manufacturing process used to create parts and components made of aluminum. The process involves injecting molten aluminum into a mold or die cavity under high pressure. Once the aluminum solidifies and cools, the mold is opened, and the part is removed.
The aluminum die casting process typically involves the following steps:
Tooling design: The first step is to design the mold or die cavity to create the desired part. The tooling design must take into account the size, shape, and complexity of the part, as well as the material properties of aluminum.
Melting: The aluminum is melted in a furnace and brought to the desired temperature.
Injection: The molten aluminum is injected into the die cavity at high pressure using a piston or plunger. This ensures that the aluminum fills the mold completely and uniformly.
Solidification: The molten aluminum solidifies and cools quickly in the die cavity, taking on the shape of the mold.
Ejection: Once the part has cooled and solidified, the mold is opened, and the part is removed from the die cavity.
Trimming and finishing: The part may require additional trimming or finishing to remove any excess material or imperfections.
Aluminum die casting is a highly efficient and precise process that allows for the creation of complex parts with tight tolerances. It is used in a wide range of industries, including automotive, aerospace, electronics, and consumer products.
Kinetic Die Casting Company
6918 Beck Avenue North Hollywood, California, 91605, USA
800-524-8083 or 818-982-9200
Use this e-mail link to send attachments: sales@kineticdc.com.