How Are Aluminum Heat Sinks Die Castings Made? Heat sinks are used to reduce or remove heat from electrical appliances. Essentially, these heat sinks are used to prevent appliances from overheating and breaking down. Currently, more and more heat sinks …
Continue reading
Various Aluminum Casting Options
Aluminum casting is a widely used manufacturing process in various industries, including automotive, aerospace, and construction. It allows for the production of complex and intricate metal parts with excellent strength-to-weight ratios. Several aluminum casting processes are available, each offering distinct advantages depending on the desired end product and production requirements. In this post, we will explore some of the most commonly used aluminum casting processes.
1. Sand Casting: This is one of the oldest and most straightforward aluminum casting processes. It involves creating a mold by compacting specially formulated sand around a pattern. Once the mold is ready, molten aluminum is poured into it, and after solidification, the sand is removed to reveal the final product.
2. Die Casting: Die casting is a high-volume production process suitable for intricate parts with consistent dimensions. Here, molten aluminum is forced into a steel mold, known as a die, using high pressure. Once solidified, the mold is opened, and the cast part is ejected.
3. Investment Casting: Also known as lost-wax casting, investment casting is ideal for producing parts with complex shapes and fine details. It involves creating a wax pattern that is coated with a ceramic shell. The wax is then melted out, leaving a hollow mold. Finally, the molten aluminum is poured into the mold and solidifies, resulting in the final part.
4. Permanent Mold Casting: In this process, a reusable mold made of steel or cast iron is used to create multiple aluminum parts. The molten aluminum is poured into the mold and allowed to solidify before the casting is extracted. Permanent mold casting offers a good balance between cost and production speed.
5. Continuous Casting: Continuous casting is primarily used for producing aluminum billets or slabs for subsequent processing. Molten aluminum is continuously poured into a water-cooled mold and solidifies as a continuous strip. This process allows for efficient mass production of aluminum in various shapes and sizes.
6. Centrifugal Casting: This process is used to produce hollow aluminum parts with good mechanical properties. Molten aluminum is poured into a rotating mold, and centrifugal forces distribute the metal along the mold’s walls, resulting in a solid, dense casting.
These are just a few of the many aluminum casting processes available today. Each process offers unique advantages and is chosen based on factors such as part complexity, production volume, cost, and desired mechanical properties. By understanding these processes, manufacturers can select the most suitable method for their specific needs and achieve high-quality aluminum castings efficiently.
“The Parts We Make Today, We Ship Today”
Kinetic Die Casting Company. Inc.
6918 Beck Avenue, North Hollywood,
California 91605, United States of America
E-mail sales@kineticdc.com
USA Toll Free: (800) 524-8083 Local: (818) 982-9200
To get prices for Die Casting Tooling Molds or Parts:
RFQ Die Casting Tooling Part Prices
Kinetic Die Casting Company makes:
Die Casting Driving Innovation
Die Casting Revolutionizes Car Parts Manufacturing, where performance, efficiency, and safety are paramount, the quality and precision of every component can make all the difference. Enter die casting, a manufacturing process that has revolutionized the production of car parts, offering unmatched precision, versatility, and efficiency. From engine components to structural elements, transmission housings to suspension components, die casting plays a pivotal role in shaping the future of automotive engineering. Let’s explore how die casting has transformed the manufacturing landscape of car parts and its profound impact on the automotive industry.
Strength and Lightweight Design. In the pursuit of fuel efficiency and performance, automotive engineers are constantly seeking ways to reduce vehicle weight without compromising strength and durability. Die casting provides an ideal solution, allowing manufacturers to produce lightweight parts with exceptional structural integrity. Aluminum and magnesium alloys, commonly used in die casting, offer a winning combination of strength and weight savings, making them well-suited for automotive applications. By leveraging die casting techniques, car manufacturers can design and fabricate components that enhance fuel efficiency, increase payload capacity, and improve overall performance.
The engine serves as the heart of any vehicle, relying on a multitude of precision-engineered components to deliver power efficiently and reliably. From cylinder heads and engine blocks to intake manifolds and transmission cases, die casting plays a critical role in the production of these vital parts. By utilizing die casting processes, automotive manufacturers can achieve the tight tolerances and intricate geometries required for optimal engine performance. Moreover, die casting enables the production of complex shapes and features that would be difficult or impossible to achieve using traditional machining methods, further enhancing engine efficiency and reliability.
Safety is a top priority in automotive design, and vehicle structures must withstand the forces encountered during normal operation and in the event of a collision. Die casting enables the production of parts with uniform grain structure and minimal porosity, resulting in enhanced mechanical properties and crashworthiness. Whether it’s chassis components, suspension parts, or body reinforcements, die-cast parts contribute to the overall strength and safety of vehicles, ensuring passenger protection and structural integrity.
The transmission and drivetrain systems are critical to the performance and efficiency of vehicles, requiring precision-engineered components to transfer power smoothly and reliably. Die casting is instrumental in the production of transmission housings, differential cases, and gearbox components, providing the strength, dimensional accuracy, and heat dissipation capabilities necessary for optimal performance. By leveraging die casting techniques, automotive manufacturers can achieve the intricate geometries and complex features required for advanced transmission systems, improving overall drivability and fuel efficiency.
As automotive technology continues to evolve, so too does the role of die casting in shaping the future of vehicle manufacturing. Manufacturers and engineers collaborate to push the boundaries of innovation, leveraging advanced materials, design optimization techniques, and cutting-edge manufacturing processes to meet the evolving needs of the automotive industry. From lightweight structural components to high-performance engine parts, die casting remains at the forefront of automotive innovation, driving progress and shaping the next generation of vehicles.
Die casting has revolutionized the manufacturing of car parts, offering automotive manufacturers the precision, efficiency, and reliability required to meet the demanding standards of the industry. From enhancing fuel efficiency to improving vehicle safety, die-cast parts play a vital role in shaping the future of automotive engineering, ensuring that vehicles continue to drive innovation and performance on the road ahead.
Permalink: https://www.kineticdiecasting.com/kdc/die-casting-driving-innovation/
“The Parts We Make Today, We Ship Today”
Kinetic Die Casting Company. Inc.
6918 Beck Avenue, North Hollywood,
California 91605, United States of America
E-mail sales@kineticdc.com
USA Toll Free: (800) 524-8083 Local: (818) 982-9200
To get prices for Die Casting Car Parts:
Quote Car Parts Die Casting Prices
Kinetic Die Casting Company makes:
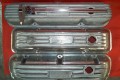
Die Casting Bracket Hardware
Airplane Die Casting Parts
Harvil Die Casting Machine for Sale
I recently purchased new LK Die Casting Machines. I have two Harvill Die Casting machines that need to be removed to make room for my new equipment. One is a 450 ton harvil the other is a 600 ton harvil. I will using the the 400 ton this week and next week. The 600 ton needs repairs before it can be used to make die casting parts. These machine are not worth a lot of money but some die casters in California have a soft spot in their heart for the Harvil brand die casting machines.
A scrap guy offered to pay me $1,500 each to cut them up and take them out. If anyone wants these machines and is willing to match that $1,500 price. Contact me, these machines can be yours. The machines need to be removed by August 2, 2024.
Kinetic Die Casting Company
6918 Beck Avenue, North Hollywood, CA
818-982-9200
sales@kineticdc.com
https://www.kineticdiecasting.com/kdc/harvil-die-casting-machine-for-sale/
More Equipment At Kineticdc
Great news for die casting part customers of Kinetic Die Casting Company. We have had great success with our new automated die casting machine this year. We have had less manufacturing production downtime, we have less die casting part porosity, we have had better die casting part product quality and we have had more reliable production die casting part quantities with this new automated die casting machine.
Over the next two months, We will be removing our older Harvil die casting machines and replacing them with automated LK die casting machines. The automated die casting machines will be in place and ready to accept new work by September 2024.
By adding more of the automated LK die casting machines to Kinetic Die Casting Company production, it will give us better die casting part quality and much more die casting part production capacity for our customers.
We will also be open to accept new manufacturing customers needing die casting parts. Contact us anytime to become one of our happy die casting part manufacturing customers.
Our contact information for die casting part quotes: Click for Die Casting Parts
https://www.kineticdiecasting.com/replyform.html
Kinetic Die Casting Company
www.kineticdiecasting.com
6918 Beck Avenue, North Hollywood, CA 91605
818-982-9200 sales@kineticdc.com
Permalink: https://www.kineticdiecasting.com/kdc/more-equipment-at-kineticdc/
Ray Fish Electro Adapter My Obituary
I always found Ray to be very intelligent, and a shrewd business man. He would be 90 years old, if he were alive today. I met Ray Fish of AQ Die Casting/Electro Adaptor on 12/11/03 when my maintenance manager, Victor Ortega, gave me his name telling me that Ray had two Toshiba die casting machines for sale, a 350ton and a 400ton with ladlers prints and manuals. The machines did not work so Ray wanted $5,000 for both die casting machines. AQ Die Casting Electro-Adaptor (https://www.electro-adapter.com/)
In 09/15/12, Ray Fish contacted me to say that he was closing down AQ Die Casting but keeping Electro Adapter. Ray sent me several dies and tooling for several customers. Since then, Ray was on my cookie and almond roca list.
On 11/11/21, I received this email from Ray regarding my Christmas almond roca update. “Thank you for the thought I lost my sweetheart and best friend 2 weeks ago to the virus 69 years of bliss. God Bless her for being there for me as always. My holidays will be memories Be Safe & Be Well, Ray”
In 1969, Ray Fish founded AQ Die Casting/Electro Adapter. Ray was involved with die castings since the 1950s. He took over operations from Barron Die Casting in the late 1960s or early 1970s.
In 1979, ten years later, he moved operations to a 54,000 square foot facility in Chatsworth, California. The Chatsworth facility, completed in 1979, is devoted to the design, development, production and qualification of connector accessories.
Electro Adapter, Inc. manufactures and supplies connector accessories, conduit assemblies, and accessory banding systems for aerospace, military, marine, railroad, and industrial automation markets. It specializes in thin-wall aluminum and zinc castings. The company offers die-castings, bulkhead adapters, extenders, connector savers, protective covers, shorting cans, banding tools, and composites; and accessories for D-sub, micro-D, circular, and ARINC rectangular connectors. It also provides casting, machining, trimming, de-burring, plating, inspection, and metal finishing services for commercial and mil spec applications; and tool and mold design and fabrication, surface treatment, painting, and assembly services. The company is based in Chatsworth, California.
Ray Fredrick Fish Obituary (2022) – FUNERAL HOME – Crawford Lorenzen Mortuary – 8717 Tampa Ave Northridge, California published on Legacy.com by Crawford Lorenzen Mortuary – Northridge on Dec. 22, 2022. (https://www.legacy.com/us/obituaries/name/ray-fish-obituary?id=38449425) Comments left on the funeral home website: January 23, 2023 and September 14, 2023
Permalink: https://www.kineticdiecasting.com/kdc/ray-fish-electro-adapter-my-obituary/