Facts about Aluminum Hardware Handles. Everybody knows that handles are very important in order to move and open hardware such as cabinets and doors. The two main types of handles are the twist handles and pull handles. Twist handles are …
Continue reading
Zinc Die Cast Brackets
Zinc die cast brackets are essential components used in various industries for a wide range of applications. Known for their high strength, durability, and precise design, these brackets play a pivotal role in providing structural support, stability, and functionality to a diverse array of products and systems. In this comprehensive guide, we will delve into the key features, benefits, applications, and considerations associated with zinc die cast brackets.
Zinc die cast brackets are manufactured using a process called die casting, which involves injecting molten zinc into a mold cavity under high pressure. This process allows for the creation of intricate and complex bracket designs with tight tolerances and uniform wall thickness. As a result, zinc die cast brackets exhibit superior dimensional accuracy and consistency, making them ideal for applications that require precise fitting and alignment.
One of the primary advantages of zinc die cast brackets is their exceptional strength-to-weight ratio. Zinc is a lightweight metal that offers excellent mechanical properties, including high tensile strength, impact resistance, and fatigue endurance. This makes zinc die cast brackets strong and rugged enough to withstand heavy loads, vibrations, and harsh environmental conditions without compromising performance or structural integrity.
Furthermore, zinc die cast brackets are corrosion-resistant, which is a critical characteristic for applications exposed to moisture, chemicals, or outdoor elements. The inherent corrosion resistance of zinc helps prevent rust and degradation, ensuring the long-term reliability and durability of the brackets in various operating environments.
In addition to their mechanical and corrosion-resistant properties, zinc die cast brackets are valued for their cost-effectiveness and versatility. The die casting process allows for mass production of brackets with minimal material waste, reducing production costs and lead times. Moreover, zinc die cast brackets can be easily customized to meet specific design requirements, such as size, shape, and mounting options, making them suitable for a wide range of applications across industries.
The automotive industry is one of the primary sectors where zinc die cast brackets find extensive use. These brackets are commonly employed in vehicle components such as engine mounts, suspension systems, and chassis assemblies, where strength, durability, and dimensional accuracy are crucial for ensuring optimal performance and safety.
In the electronics and telecommunications sector, zinc die cast brackets are utilized in the manufacturing of mounting hardware for electronic devices, communication equipment, and networking systems. The precise design and reliable performance of zinc die cast brackets help secure components in place and support the overall functionality of these devices.
Moreover, zinc die cast brackets are widely used in the construction, furniture, and consumer goods industries for applications ranging from shelf supports and furniture fittings to lighting fixtures and display systems. Their versatility, strength, and cost-effectiveness make them a preferred choice for manufacturers seeking durable and high-quality bracket solutions.
When selecting zinc die cast brackets for your applications, it is essential to consider factors such as load capacity, installation requirements, environmental conditions, and regulatory compliance. By choosing high-quality zinc die cast brackets from reputable manufacturers and suppliers, you can ensure the reliability, performance, and longevity of your products and systems.
In conclusion, zinc die cast brackets are essential components that offer a combination of strength, durability, precision, and versatility for a wide range of industrial applications. Their exceptional mechanical properties, corrosion resistance, cost-effectiveness, and customization options make them an ideal choice for manufacturers seeking reliable and high-performance bracket solutions. Whether in automotive, electronics, construction, or consumer goods, zinc die cast brackets play a vital role in enhancing the functionality, safety, and quality of products and systems across diverse industries.
“The Parts We Make Today, We Ship Today”
Kinetic Die Casting Company. Inc.
6918 Beck Avenue, North Hollywood,
California 91605, United States of America
E-mail sales@kineticdc.com
USA Toll Free: (800) 524-8083 Local: (818) 982-9200
To get prices for Die Casting Tooling Molds or Parts:
RFQ Die Casting Tooling Part Prices
Kinetic Die Casting Company makes:
What Are Die Casting Parts?
Die Casting Aluminum Heat Sinks
Aluminum Boxes Diecastings
Sponsored Listings:
House in Florida
Manufacturing Excellence in California
The State of California USA, renowned for its innovation, diversity, and entrepreneurial spirit, stands as a beacon of manufacturing excellence within the United States. From cutting-edge technology and aerospace advancements to sustainable practices and artisanal craftsmanship, the state’s manufacturing sector encompasses a broad spectrum of industries, each contributing to its vibrant and dynamic economy. Let’s explore the multifaceted landscape of manufacturing in California and the factors that have propelled its growth and success. Manufacturing Excellence: The Dynamic Landscape of Manufacturing in California
California’s manufacturing sector spans a diverse array of industries, reflecting the state’s rich tapestry of innovation and creativity. From Silicon Valley’s high-tech giants and biotech innovators to Southern California’s aerospace pioneers and Central Valley’s agricultural powerhouses, California is home to a multitude of manufacturing hubs driving progress and prosperity across the state and beyond. Whether it’s advanced electronics, sustainable energy solutions, precision machinery, or artisanal goods, California’s manufacturing prowess knows no bounds.
Innovation and Technology Leadership, at the forefront of innovation and technology, California’s manufacturing sector continually pushes the boundaries of what’s possible. Silicon Valley, situated in the San Francisco Bay Area, serves as the epicenter of technological innovation, driving advancements in semiconductors, software development, and digital manufacturing. With a concentration of world-class research institutions, venture capital firms, and entrepreneurial talent, California remains a global leader in fostering innovation and nurturing startups that are revolutionizing the manufacturing landscape.
Aerospace and Defense Manufacturing Excellence, Southern California boasts a rich heritage in aerospace and defense manufacturing, with iconic companies such as Boeing, Lockheed Martin, and Northrop Grumman calling the region home. From designing and manufacturing cutting-edge aircraft and spacecraft to developing advanced defense systems and components, California’s aerospace industry continues to push the boundaries of aerospace engineering and innovation. With a skilled workforce, robust supply chain, and close collaboration with government agencies and research institutions, California remains a vital hub for aerospace manufacturing excellence.
Sustainability and Green Manufacturing, California leads the nation in embracing sustainable manufacturing practices and green technologies aimed at reducing environmental impact and promoting sustainability. From renewable energy solutions and zero-emission vehicles to eco-friendly packaging and waste reduction initiatives, manufacturers across the state are pioneering innovative approaches to mitigate climate change and create a more sustainable future. With stringent environmental regulations and a commitment to corporate social responsibility, California’s manufacturing sector serves as a global model for sustainable and responsible production practices.
Skilled Workforce and Education Initiatives, California’s manufacturing success is underpinned by its highly skilled and diverse workforce, supported by a robust network of educational institutions, vocational training programs, and workforce development initiatives. From community colleges and technical schools to apprenticeship programs and industry partnerships, California invests in preparing the next generation of manufacturing talent, ensuring a steady pipeline of skilled workers equipped to meet the evolving needs of the industry. Additionally, initiatives promoting diversity, equity, and inclusion are fostering a more inclusive and equitable manufacturing workforce reflective of California’s diverse population.
Global Connectivity and Trade, As a global economic powerhouse, California benefits from its strategic location and robust trade connections, serving as a gateway to international markets. With world-class ports, airports, and logistics infrastructure, California facilitates the movement of goods and services to and from key markets around the world. International trade agreements and partnerships further enhance California’s position as a global manufacturing hub, facilitating the exchange of ideas, technologies, and resources that drive innovation and economic growth. Manufacturing in California is characterized by innovation, diversity, and a relentless pursuit of excellence. From technological breakthroughs and aerospace advancements to sustainability initiatives and workforce development, California’s manufacturing sector continues to shape the future of industry and drive economic prosperity both within the state and beyond. As innovation and collaboration thrive, California remains at the forefront of manufacturing innovation, paving the way for a brighter, more sustainable future.
“The Parts We Make Today, We Ship Today”
Kinetic Die Casting Company. Inc.
6918 Beck Avenue, North Hollywood,
California 91605, United States of America
E-mail sales@kineticdc.com
USA Toll Free: (800) 524-8083 Local: (818) 982-9200
To get prices for Die Casting Tooling Molds or Parts:
RFQ Die Casting Tooling Part Prices
Kinetic Die Casting Company makes:
Die Casting Business
Die Casting Manufacturing
Various Aluminum Casting Options
Aluminum casting is a widely used manufacturing process in various industries, including automotive, aerospace, and construction. It allows for the production of complex and intricate metal parts with excellent strength-to-weight ratios. Several aluminum casting processes are available, each offering distinct advantages depending on the desired end product and production requirements. In this post, we will explore some of the most commonly used aluminum casting processes.
1. Sand Casting: This is one of the oldest and most straightforward aluminum casting processes. It involves creating a mold by compacting specially formulated sand around a pattern. Once the mold is ready, molten aluminum is poured into it, and after solidification, the sand is removed to reveal the final product.
2. Die Casting: Die casting is a high-volume production process suitable for intricate parts with consistent dimensions. Here, molten aluminum is forced into a steel mold, known as a die, using high pressure. Once solidified, the mold is opened, and the cast part is ejected.
3. Investment Casting: Also known as lost-wax casting, investment casting is ideal for producing parts with complex shapes and fine details. It involves creating a wax pattern that is coated with a ceramic shell. The wax is then melted out, leaving a hollow mold. Finally, the molten aluminum is poured into the mold and solidifies, resulting in the final part.
4. Permanent Mold Casting: In this process, a reusable mold made of steel or cast iron is used to create multiple aluminum parts. The molten aluminum is poured into the mold and allowed to solidify before the casting is extracted. Permanent mold casting offers a good balance between cost and production speed.
5. Continuous Casting: Continuous casting is primarily used for producing aluminum billets or slabs for subsequent processing. Molten aluminum is continuously poured into a water-cooled mold and solidifies as a continuous strip. This process allows for efficient mass production of aluminum in various shapes and sizes.
6. Centrifugal Casting: This process is used to produce hollow aluminum parts with good mechanical properties. Molten aluminum is poured into a rotating mold, and centrifugal forces distribute the metal along the mold’s walls, resulting in a solid, dense casting.
These are just a few of the many aluminum casting processes available today. Each process offers unique advantages and is chosen based on factors such as part complexity, production volume, cost, and desired mechanical properties. By understanding these processes, manufacturers can select the most suitable method for their specific needs and achieve high-quality aluminum castings efficiently.
“The Parts We Make Today, We Ship Today”
Kinetic Die Casting Company. Inc.
6918 Beck Avenue, North Hollywood,
California 91605, United States of America
E-mail sales@kineticdc.com
USA Toll Free: (800) 524-8083 Local: (818) 982-9200
To get prices for Die Casting Tooling Molds or Parts:
RFQ Die Casting Tooling Part Prices
Kinetic Die Casting Company makes:
Die Casting Driving Innovation
Die Casting Revolutionizes Car Parts Manufacturing, where performance, efficiency, and safety are paramount, the quality and precision of every component can make all the difference. Enter die casting, a manufacturing process that has revolutionized the production of car parts, offering unmatched precision, versatility, and efficiency. From engine components to structural elements, transmission housings to suspension components, die casting plays a pivotal role in shaping the future of automotive engineering. Let’s explore how die casting has transformed the manufacturing landscape of car parts and its profound impact on the automotive industry.
Strength and Lightweight Design. In the pursuit of fuel efficiency and performance, automotive engineers are constantly seeking ways to reduce vehicle weight without compromising strength and durability. Die casting provides an ideal solution, allowing manufacturers to produce lightweight parts with exceptional structural integrity. Aluminum and magnesium alloys, commonly used in die casting, offer a winning combination of strength and weight savings, making them well-suited for automotive applications. By leveraging die casting techniques, car manufacturers can design and fabricate components that enhance fuel efficiency, increase payload capacity, and improve overall performance.
The engine serves as the heart of any vehicle, relying on a multitude of precision-engineered components to deliver power efficiently and reliably. From cylinder heads and engine blocks to intake manifolds and transmission cases, die casting plays a critical role in the production of these vital parts. By utilizing die casting processes, automotive manufacturers can achieve the tight tolerances and intricate geometries required for optimal engine performance. Moreover, die casting enables the production of complex shapes and features that would be difficult or impossible to achieve using traditional machining methods, further enhancing engine efficiency and reliability.
Safety is a top priority in automotive design, and vehicle structures must withstand the forces encountered during normal operation and in the event of a collision. Die casting enables the production of parts with uniform grain structure and minimal porosity, resulting in enhanced mechanical properties and crashworthiness. Whether it’s chassis components, suspension parts, or body reinforcements, die-cast parts contribute to the overall strength and safety of vehicles, ensuring passenger protection and structural integrity.
The transmission and drivetrain systems are critical to the performance and efficiency of vehicles, requiring precision-engineered components to transfer power smoothly and reliably. Die casting is instrumental in the production of transmission housings, differential cases, and gearbox components, providing the strength, dimensional accuracy, and heat dissipation capabilities necessary for optimal performance. By leveraging die casting techniques, automotive manufacturers can achieve the intricate geometries and complex features required for advanced transmission systems, improving overall drivability and fuel efficiency.
As automotive technology continues to evolve, so too does the role of die casting in shaping the future of vehicle manufacturing. Manufacturers and engineers collaborate to push the boundaries of innovation, leveraging advanced materials, design optimization techniques, and cutting-edge manufacturing processes to meet the evolving needs of the automotive industry. From lightweight structural components to high-performance engine parts, die casting remains at the forefront of automotive innovation, driving progress and shaping the next generation of vehicles.
Die casting has revolutionized the manufacturing of car parts, offering automotive manufacturers the precision, efficiency, and reliability required to meet the demanding standards of the industry. From enhancing fuel efficiency to improving vehicle safety, die-cast parts play a vital role in shaping the future of automotive engineering, ensuring that vehicles continue to drive innovation and performance on the road ahead.
Permalink: https://www.kineticdiecasting.com/kdc/die-casting-driving-innovation/
“The Parts We Make Today, We Ship Today”
Kinetic Die Casting Company. Inc.
6918 Beck Avenue, North Hollywood,
California 91605, United States of America
E-mail sales@kineticdc.com
USA Toll Free: (800) 524-8083 Local: (818) 982-9200
To get prices for Die Casting Car Parts:
Quote Car Parts Die Casting Prices
Kinetic Die Casting Company makes:
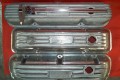
Die Casting Bracket Hardware
Airplane Die Casting Parts
Harvil Die Casting Machine for Sale
I recently purchased new LK Die Casting Machines. I have two Harvill Die Casting machines that need to be removed to make room for my new equipment. One is a 450 ton harvil the other is a 600 ton harvil. I will using the the 400 ton this week and next week. The 600 ton needs repairs before it can be used to make die casting parts. These machine are not worth a lot of money but some die casters in California have a soft spot in their heart for the Harvil brand die casting machines.
A scrap guy offered to pay me $1,500 each to cut them up and take them out. If anyone wants these machines and is willing to match that $1,500 price. Contact me, these machines can be yours. The machines need to be removed by August 2, 2024.
Kinetic Die Casting Company
6918 Beck Avenue, North Hollywood, CA
818-982-9200
sales@kineticdc.com
https://www.kineticdiecasting.com/kdc/harvil-die-casting-machine-for-sale/