Aluminum boxes are needed by many industries including the military. Enclosure castings and Housing castings are aluminum box castings or aluminum die casting parts. These enclosures are typically designed to hold electronic components into place using a printed circuit board …
Continue reading
Tag Archives: #AluminumParts
Die Casting Driving Innovation
Die Casting Revolutionizes Car Parts Manufacturing, where performance, efficiency, and safety are paramount, the quality and precision of every component can make all the difference. Enter die casting, a manufacturing process that has revolutionized the production of car parts, offering unmatched precision, versatility, and efficiency. From engine components to structural elements, transmission housings to suspension components, die casting plays a pivotal role in shaping the future of automotive engineering. Let’s explore how die casting has transformed the manufacturing landscape of car parts and its profound impact on the automotive industry.
Strength and Lightweight Design. In the pursuit of fuel efficiency and performance, automotive engineers are constantly seeking ways to reduce vehicle weight without compromising strength and durability. Die casting provides an ideal solution, allowing manufacturers to produce lightweight parts with exceptional structural integrity. Aluminum and magnesium alloys, commonly used in die casting, offer a winning combination of strength and weight savings, making them well-suited for automotive applications. By leveraging die casting techniques, car manufacturers can design and fabricate components that enhance fuel efficiency, increase payload capacity, and improve overall performance.
The engine serves as the heart of any vehicle, relying on a multitude of precision-engineered components to deliver power efficiently and reliably. From cylinder heads and engine blocks to intake manifolds and transmission cases, die casting plays a critical role in the production of these vital parts. By utilizing die casting processes, automotive manufacturers can achieve the tight tolerances and intricate geometries required for optimal engine performance. Moreover, die casting enables the production of complex shapes and features that would be difficult or impossible to achieve using traditional machining methods, further enhancing engine efficiency and reliability.
Safety is a top priority in automotive design, and vehicle structures must withstand the forces encountered during normal operation and in the event of a collision. Die casting enables the production of parts with uniform grain structure and minimal porosity, resulting in enhanced mechanical properties and crashworthiness. Whether it’s chassis components, suspension parts, or body reinforcements, die-cast parts contribute to the overall strength and safety of vehicles, ensuring passenger protection and structural integrity.
The transmission and drivetrain systems are critical to the performance and efficiency of vehicles, requiring precision-engineered components to transfer power smoothly and reliably. Die casting is instrumental in the production of transmission housings, differential cases, and gearbox components, providing the strength, dimensional accuracy, and heat dissipation capabilities necessary for optimal performance. By leveraging die casting techniques, automotive manufacturers can achieve the intricate geometries and complex features required for advanced transmission systems, improving overall drivability and fuel efficiency.
As automotive technology continues to evolve, so too does the role of die casting in shaping the future of vehicle manufacturing. Manufacturers and engineers collaborate to push the boundaries of innovation, leveraging advanced materials, design optimization techniques, and cutting-edge manufacturing processes to meet the evolving needs of the automotive industry. From lightweight structural components to high-performance engine parts, die casting remains at the forefront of automotive innovation, driving progress and shaping the next generation of vehicles.
Die casting has revolutionized the manufacturing of car parts, offering automotive manufacturers the precision, efficiency, and reliability required to meet the demanding standards of the industry. From enhancing fuel efficiency to improving vehicle safety, die-cast parts play a vital role in shaping the future of automotive engineering, ensuring that vehicles continue to drive innovation and performance on the road ahead.
Permalink: https://www.kineticdiecasting.com/kdc/die-casting-driving-innovation/
“The Parts We Make Today, We Ship Today”
Kinetic Die Casting Company. Inc.
6918 Beck Avenue, North Hollywood,
California 91605, United States of America
E-mail sales@kineticdc.com
USA Toll Free: (800) 524-8083 Local: (818) 982-9200
To get prices for Die Casting Car Parts:
Quote Car Parts Die Casting Prices
Kinetic Die Casting Company makes:
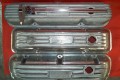
Die Casting Bracket Hardware
Airplane Die Casting Parts
The Importance of Die Casting Draft Angles
In die casting, when precision meets efficiency, every detail matters. Among the many factors that contribute to the success of the die casting process, the draft angle stands out as a crucial consideration. Often overlooked but essential, the draft angle plays a pivotal role in ensuring the manufacturability, quality, and integrity of die-cast parts. Let’s delve into the significance of draft angles in die casting and the strategies employed to optimize their impact on the production process.
Understanding Draft Angles in die casting, a draft angle refers to the taper or slope applied to vertical walls or surfaces of a mold cavity. It facilitates the removal of the casting from the mold after the casting process is complete. By incorporating draft angles into the design of die-cast parts, manufacturers can prevent damage to the part and the mold, reduce the likelihood of defects, and ensure smoother ejection during demolding. The primary function of draft angles is to facilitate the ejection of the casting from the mold cavity. Without proper draft angles, the casting may become wedged or stuck within the mold, leading to deformation, surface defects, or even mold damage during the demolding process. By providing a gradual taper to the walls of the mold, draft angles allow for easy and consistent removal of the casting, minimizing the risk of costly rework or production delays. Draft angles also play a crucial role in preventing undercuts, which occur when features of the part prevent it from being extracted straight out of the mold. Without adequate draft angles, undercuts can result in the formation of undesirable features such as flash or distortion on the casting, compromising its dimensional accuracy and surface finish. By incorporating draft angles into the design, engineers can mitigate the risk of undercuts and ensure smooth demolding of the part. Proper draft angles contribute to the overall surface finish of die-cast parts. By allowing for smooth ejection from the mold cavity, draft angles help minimize friction and shear forces that can result in surface imperfections such as scratches, blemishes, or parting lines. Additionally, draft angles promote uniform cooling of the casting, reducing the likelihood of thermal gradients and associated defects, thus enhancing the final surface quality of the part.
While draft angles are primarily functional considerations, they also have implications for the aesthetics of die-cast parts. Careful attention to draft angles can help maintain the visual integrity of the part by minimizing the appearance of parting lines, flash, or other defects. By striking the right balance between functionality and aesthetics, designers can ensure that die-cast parts not only perform optimally but also meet the visual standards expected by customers.
Die Casting Draft Angles are a critical aspect of die casting design, influencing the manufacturability, quality, and aesthetics of die-cast parts. By incorporating proper draft angles into the design process, manufacturers can optimize the die casting process, minimize production issues, and ensure the successful production of high-quality parts. As die casting continues to evolve and innovate, draft angles will remain an essential consideration in achieving precision, efficiency, and excellence in manufacturing.
“The Parts We Make Today, We Ship Today”
Kinetic Die Casting Company. Inc.
6918 Beck Avenue, North Hollywood,
California 91605, United States of America
E-mail sales@kineticdc.com
USA Toll Free: (800) 524-8083 Local: (818) 982-9200
To get prices for Die Casting Parts:
Request Die Casting Part Prices
Kinetic Die Casting Company makes:
NADCA-Product-Standards-for-Die-Casting-pdf
Die Casting Porosity
Die Casting Draft Angle
The Pursuit of Die Casting Quality
In the realm of manufacturing, quality reigns supreme. Whether it’s automotive components, electronic enclosures, or consumer goods, the reliability and performance of products hinge upon the precision and integrity of their parts. In this context, die casting emerges as a stalwart process, renowned for its ability to produce high-quality metal components with unparalleled accuracy and consistency. Let’s explore the nuances of die casting quality and the measures undertaken to uphold excellence in this dynamic field. At the heart of die casting quality lies precision engineering. Die casting involves the injection of molten metal into precisely crafted molds under high pressure, resulting in intricate parts with tight tolerances. From intricate geometries to complex features, die casting techniques excel in delivering components with utmost accuracy, meeting the stringent specifications demanded by diverse industries. Quality in die casting begins with the selection of materials. Aluminum, zinc, and magnesium alloys are commonly employed due to their exceptional properties, including high strength, lightweight, and corrosion resistance. The choice of alloy, coupled with stringent quality control measures, ensures that die-cast components exhibit optimal performance characteristics, meeting the requirements of even the most demanding applications.
Central to achieving die casting quality is rigorous quality control throughout the manufacturing process. From material inspection and die design validation to process monitoring and post-casting inspection, each stage is meticulously scrutinized to detect and rectify any deviations from the desired specifications. Advanced technologies such as X-ray inspection, dimensional analysis, and metallurgical testing play a pivotal role in ensuring that every part meets the highest standards of quality and reliability.
The pursuit of die casting quality is an ongoing journey marked by continuous improvement initiatives. Manufacturers invest in research and development to refine die casting processes, optimize tooling designs, and enhance material properties. By leveraging cutting-edge technologies and best practices, they strive to push the boundaries of quality excellence, driving innovation and raising the bar for industry standards. Traceability is a cornerstone of die casting quality, enabling manufacturers to track the entire lifecycle of each component, from raw material procurement to final assembly. By maintaining comprehensive records and implementing robust quality management systems, manufacturers uphold accountability and transparency, instilling confidence in the reliability and integrity of their products. Ultimately, die casting quality is intrinsically linked to customer satisfaction. Manufacturers prioritize understanding the unique requirements and expectations of their clients, collaborating closely to deliver customized solutions that meet or exceed their specifications. By fostering strong partnerships and embracing a customer-centric ethos, manufacturers forge lasting relationships built on trust, reliability, and mutual success. Die casting quality is not merely a benchmark to be achieved but a relentless pursuit of perfection. It embodies a commitment to precision, integrity, and continuous improvement, underpinning the foundation of modern manufacturing. As industries evolve and demand for high-quality metal components grows, the unwavering dedication to die casting quality ensures that products remain at the forefront of innovation, performance, and reliability.
“The Parts We Make Today, We Ship Today”
Kinetic Die Casting Company. Inc.
6918 Beck Avenue, North Hollywood,
California 91605, United States of America
E-mail sales@kineticdc.com
USA Toll Free: (800) 524-8083 Local: (818) 982-9200
o get prices for Die Casting Tooling Molds or Parts:
Quote Die Casting Lighting Part Prices
Kinetic Die Casting Company makes:
Light Fixture Die Casting Parts
Photos Die Casting Parts
Aerospace Die Casting Parts
Permalink: https://www.kineticdiecasting.com/kdc/the-pursuit-of-die-casting-quality/
B. Bunch Company Closed
Kinetic Die Casting Company first started making aluminum die casting parts for B. Bunch in 2004 when C&D Die Casting Company Closed. B. Bunch Company would buy about 500 aluminum die casting parts a year or every two years. Last year, 2023, I received a call telling me that B. Bunch would be closing. I was again very sad that a great American manufacturing company would be closing. Parts can still be purchased from this website https://kbfolderparts.com/
Die Casting Aluminum Part
Information from their old website: (http://bbunch.com/)
Parts can still be purchased from this website https://kbfolderparts.com/
B Bunch Co., Inc.
9619 N 21st Drive
Phoenix, AZ 85021-1895
USA
phone 602-997-6452
fax 602-997-7266
“B. Bunch Co., Inc. shipped its first fan folding machine on April 21, 1968. Since then, the product line has expanded to more than 60 different machine types including more than 30 styles of Folders, and several different types of Sheeters, Unwinds, Rewinds, Processors as well as specialized accessory printing equipment. More than 7,500 machines have been supplied to forms and label companies, and specialized printing, paper processing plants, and data centers world- wide.”
B. Bunch, as a manufacturing company customer, always paid their invoices for die casting parts timely. B.Bunch gave very good feedback on their production part’s needs and communicated very well with our company, Kinetic Die Casting Company. We will miss the company and the people that worked there.
Kinetic Die Casting Company, Inc.
6918 Beck Avenue, North Hollywood, CA 91605 USA sales@kineticdc.com
Permalink: https://www.kineticdiecasting.com/kdc/b-bunch-company-closed/
Aluminum Cast Parts are Widely Used in 2024
In the world of manufacturing and engineering, aluminum cast parts play a crucial role in creating a wide range of products. From automotive components to aerospace parts, aluminum castings are highly valued for their versatility, durability, and cost-effectiveness. In this blog post, we will delve into the reasons why aluminum cast parts are widely used in various industries across the globe.
What Are Die Casting Parts?
Aluminum is a lightweight metal known for its excellent strength-to-weight ratio, making it an ideal material for producing cast parts that need to be both sturdy and lightweight. Through the casting process, aluminum can be shaped into complex geometries with precision and accuracy, allowing for the creation of components that are tailored to specific requirements. This versatility in design is a key advantage of aluminum cast parts, as it enables manufacturers to produce parts that are both functional and aesthetically pleasing.
One of the main reasons why aluminum cast parts are favored in the manufacturing industry is their cost-effectiveness. Aluminum is abundant and relatively inexpensive compared to other metals, making it a cost-effective option for producing a wide range of components. Furthermore, the casting process itself is efficient and requires minimal post-processing, reducing production time and costs. This makes aluminum cast parts an attractive choice for companies looking to optimize their manufacturing processes without compromising on quality.
Another factor that contributes to the widespread use of aluminum cast parts is their excellent corrosion resistance. Aluminum naturally forms a protective oxide layer on its surface, which helps prevent rust and corrosion, making it ideal for applications in harsh environments or exposed to the elements. This corrosion resistance ensures the longevity of aluminum cast parts, reducing maintenance costs and extending the lifespan of products.
Furthermore, aluminum cast parts offer excellent thermal conductivity, making them ideal for applications that require heat dissipation or thermal management. This property is particularly valuable in industries such as automotive, aerospace, and electronics, where efficient heat transfer is essential for optimal performance and safety. By utilizing aluminum cast parts, manufacturers can ensure that their products operate at peak efficiency while maintaining stable temperatures.
In addition to their mechanical properties, aluminum cast parts are also highly recyclable, making them a sustainable choice for environmentally conscious companies. Aluminum is endlessly recyclable without losing its inherent properties, reducing the demand for primary aluminum production and lowering carbon emissions. By choosing aluminum castings, manufacturers can contribute to a more sustainable future while meeting their production needs.
Aluminum cast parts are widely used in various industries due to their exceptional properties, cost-effectiveness, and sustainability. Whether it’s for automotive components, aerospace structures, or consumer electronics, aluminum castings offer a myriad of benefits that make them a preferred choice for manufacturers worldwide. As technology advances and industries evolve, aluminum cast parts will continue to play a vital role in shaping the products we rely on every day.
“The Parts We Make Today, We Ship Today”
Kinetic Die Casting Company. Inc.
6918 Beck Avenue, North Hollywood,
California 91605, United States of America
E-mail sales@kineticdc.com
USA Toll Free: (800) 524-8083 Local: (818) 982-9200
To get prices for Die Casting Tooling Molds or Parts:
RFQ Die Casting Tooling Part Prices
Kinetic Die Casting Company makes:
Die Casting Aluminum Heat Sinks
Aluminum Boxes Diecastings