Spending Less on Aircraft Parts with New Aerospace Die Castings. In the aircraft industry, the cast aluminum metal has established a wide application in the production of both major and minor component parts. It has long been utilized in this …
Continue reading
Tag Archives: #CarParts
Revolutionizing Automotive Engineering
Aluminum Car Part Die Castings are used where efficiency, performance, and safety are important, the choice of materials and manufacturing processes plays a critical role in shaping the future of vehicle design. Among the myriad manufacturing techniques available, aluminum die casting stands out as a game-changer, offering unparalleled versatility, strength, and efficiency in producing car parts. From engine components to structural elements, aluminum die castings have revolutionized automotive engineering, driving innovation and excellence in vehicle manufacturing. Let’s delve into the significance of aluminum car part die castings and explore their transformative impact on the automotive industry.
Aluminum die casting enables the production of automotive parts with intricate geometries, tight tolerances, and complex features that would be challenging or cost-prohibitive to achieve using traditional manufacturing methods. Through advanced die casting techniques such as high-pressure die casting (HPDC) and vacuum die casting, automotive engineers can create components with superior dimensional accuracy, surface finish, and mechanical properties. This precision engineering translates into enhanced performance, reliability, and durability of vehicle systems, contributing to a smoother, more responsive driving experience for consumers.
As the automotive industry continues to prioritize sustainability and environmental responsibility, aluminum die casting emerges as a preferred manufacturing solution due to its eco-friendly properties. Aluminum is highly recyclable, with the ability to be melted down and reused indefinitely without compromising its mechanical properties. By incorporating recycled aluminum into die casting processes, automakers can reduce energy consumption, greenhouse gas emissions, and raw material extraction, contributing to a more sustainable and circular economy.
Aluminum car part die castings have revolutionized automotive engineering, offering a winning combination of lightweight design, precision engineering, durability, and sustainability. As automakers continue to innovate and push the boundaries of vehicle design and performance, aluminum die casting will remain a cornerstone technology, driving progress and excellence in the automotive industry. From fuel-efficient engines to sleek body designs, aluminum die castings are shaping the future of mobility, delivering vehicles that are safer, more efficient, and more environmentally friendly.
“The Parts We Make Today, We Ship Today”
Kinetic Die Casting Company. Inc.
6918 Beck Avenue, North Hollywood,
California 91605, United States of America
E-mail sales@kineticdc.com
USA Toll Free: (800) 524-8083 Local: (818) 982-9200
To get prices for Die Casting Car Parts:
Quote Prices for Die Casting Car Parts/font>
Kinetic Die Casting Company makes:
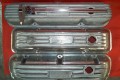
Die Casting Bracket Hardware
Airplane Die Casting Parts
Die Casting Driving Innovation
Die Casting Revolutionizes Car Parts Manufacturing, where performance, efficiency, and safety are paramount, the quality and precision of every component can make all the difference. Enter die casting, a manufacturing process that has revolutionized the production of car parts, offering unmatched precision, versatility, and efficiency. From engine components to structural elements, transmission housings to suspension components, die casting plays a pivotal role in shaping the future of automotive engineering. Let’s explore how die casting has transformed the manufacturing landscape of car parts and its profound impact on the automotive industry.
Strength and Lightweight Design. In the pursuit of fuel efficiency and performance, automotive engineers are constantly seeking ways to reduce vehicle weight without compromising strength and durability. Die casting provides an ideal solution, allowing manufacturers to produce lightweight parts with exceptional structural integrity. Aluminum and magnesium alloys, commonly used in die casting, offer a winning combination of strength and weight savings, making them well-suited for automotive applications. By leveraging die casting techniques, car manufacturers can design and fabricate components that enhance fuel efficiency, increase payload capacity, and improve overall performance.
The engine serves as the heart of any vehicle, relying on a multitude of precision-engineered components to deliver power efficiently and reliably. From cylinder heads and engine blocks to intake manifolds and transmission cases, die casting plays a critical role in the production of these vital parts. By utilizing die casting processes, automotive manufacturers can achieve the tight tolerances and intricate geometries required for optimal engine performance. Moreover, die casting enables the production of complex shapes and features that would be difficult or impossible to achieve using traditional machining methods, further enhancing engine efficiency and reliability.
Safety is a top priority in automotive design, and vehicle structures must withstand the forces encountered during normal operation and in the event of a collision. Die casting enables the production of parts with uniform grain structure and minimal porosity, resulting in enhanced mechanical properties and crashworthiness. Whether it’s chassis components, suspension parts, or body reinforcements, die-cast parts contribute to the overall strength and safety of vehicles, ensuring passenger protection and structural integrity.
The transmission and drivetrain systems are critical to the performance and efficiency of vehicles, requiring precision-engineered components to transfer power smoothly and reliably. Die casting is instrumental in the production of transmission housings, differential cases, and gearbox components, providing the strength, dimensional accuracy, and heat dissipation capabilities necessary for optimal performance. By leveraging die casting techniques, automotive manufacturers can achieve the intricate geometries and complex features required for advanced transmission systems, improving overall drivability and fuel efficiency.
As automotive technology continues to evolve, so too does the role of die casting in shaping the future of vehicle manufacturing. Manufacturers and engineers collaborate to push the boundaries of innovation, leveraging advanced materials, design optimization techniques, and cutting-edge manufacturing processes to meet the evolving needs of the automotive industry. From lightweight structural components to high-performance engine parts, die casting remains at the forefront of automotive innovation, driving progress and shaping the next generation of vehicles.
Die casting has revolutionized the manufacturing of car parts, offering automotive manufacturers the precision, efficiency, and reliability required to meet the demanding standards of the industry. From enhancing fuel efficiency to improving vehicle safety, die-cast parts play a vital role in shaping the future of automotive engineering, ensuring that vehicles continue to drive innovation and performance on the road ahead.
Permalink: https://www.kineticdiecasting.com/kdc/die-casting-driving-innovation/
“The Parts We Make Today, We Ship Today”
Kinetic Die Casting Company. Inc.
6918 Beck Avenue, North Hollywood,
California 91605, United States of America
E-mail sales@kineticdc.com
USA Toll Free: (800) 524-8083 Local: (818) 982-9200
To get prices for Die Casting Car Parts:
Quote Car Parts Die Casting Prices
Kinetic Die Casting Company makes:
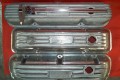
Die Casting Bracket Hardware
Airplane Die Casting Parts