MOUNT GILEAD, OHIO — Former HPM owner Christopher Filos pleaded guilty to the company’s failure to pay taxes on Aug. 21, just days before his trial was scheduled to begin in Morrow County Common Pleas Court. Filos, 47, signed off …
Continue reading
Tag Archives: Die Casting Company
Metal Die Cast in the Cold Chamber
Metal Die Cast in the Cold Chamber. In the field of metallurgy, the cold chamber method is known as one of the two chief types of die casting processes. The other one is called the hot chamber method. If you noticed sculpted metal parts with a high melting point, they are in all probability fashioned by a cold chamber machine. Cold chamber die castings could be created out of aluminum, magnesium die casting, and copper.
These cold chamber die castings go through outside furnaces. The metals are then poured into a cold chamber in the machine. The cylinder and plunger are not submerged in liquefied metal as is the method with low melting point metal alloys in a hot chamber method. These enormous machines use hydraulic power to force the poured metal into the die mold. It is a slower procedure but the machines utilized for cold chamber die castings usually last longer. This and its capability to manufacture metals with a high melting point into exactitude parts make it helpful for machinists, metallurgists, metalworkers, engineers, and manufacturers of our modern gadgets like aluminum die cast boxes that are utilized in electrical outlets and other such electrical fixtures.
Die casting is only one of the procedures utilized to shape metal to our wants. There is also forging, rolling, sintering, machining, fabrication, metalworking, and numerous other different casting procedures. Then there are the practices of fusing one metal to another which are soldering, welding, and brazing. There are also other procedures such as annealing, tempering, quenching, plating, thermal spraying, and case hardening. All these metalworking methods have given to the development of our world as we know it today.
Kinetic Die Casting makes great quality aluminum, and Zinc Die Casting If looking for a job or would like a quote please visit our website:Kinetic Die Casting Company
Different Forms of Die Casting Tooling
Different Forms of Die Casting Tooling. Die casting tooling can also be dubbed insert die, die casting molds, or die casting dies. They can come in a variety of forms, styles, and sizes. One of the shapes of die casting tooling is the die cast tooling inserts. They are the least pricey among the tooling that needs heat-treating so that the life of the insert will be extended. The tooling life is the number of parts probable to be completed in the inserts. The other form is the Prototype die casting tooling insert. They are the same with the first form of tooling but the only dissimilarity is that this type require not be heat-treated and can be broken easily.
The next type is die casting unit die tooling and this is smaller than the total mold but better than the inserts. It also uses more steel compared to the inserts and less steel than the complete mold.
Complete Class A die casting die fits into the die casting machine without the use of any base or holder. This type creates better quality parts and more die life. It has waterlines and trim dies that can speed up the manufacturing.
Die casting Family Mold tooling has several cavity die inserts that can process single or multiple parts each cycle. It should be detached from the machine when changing inserts so it is expensive and not time proficient.
Trim dies can save time in production and cut the surplus alloy in the parts shaped. They are mounted into a trim press and are pressed together with tons of pressure.
Kinetic Die Casting can manufacture aluminum automobile parts, heat sinks, aerospace parts and much more. If you are looking for aluminum or zinc parts, visit our website Kinetic Die Casting Company
Die Casting Part Prices
Kinetic Die Casting Company discusses how Die Casting Part Prices are determined. A die casting company is sometimes also known as a Job Shop Manufacturer. In other words, the die casting company provides metal products to other manufacturing companies. These other manufacturing companies, sometimes are OEMs (Original Equipment Manufacturers). These die casting metal products, die castings, are used in the product produced by the OEM customer, who is always a manufacturing company.
Die casting part prices or diecastings prices are determined using only a few factors.
- Utilities Costs (Water, Gas and Electric)
- Overhead and Fixed Costs
- The Cost of Labor Rates
- The Number of Labor Hours
- Setup Costs for equipment and die casting molds
- Die Casting Metal Amounts
- Die Casting Metal Cost Each Pound
- Value Added Processes.
All of these variables listed to manufacture die casting parts. Typically die castings cost less than $1.00 to $5.00 each die casting part.
- Utilities Costs – Are used to melt the die casting metal for two or four hours prior to die casting production. The high pressure die casting machines use a lot of electricity to operate the high pressure pumps.
- Overhead and Fixed Costs – These are costs that are frequently overlooked, such as Rent, Insurance, Medical Benefits and Salaries for Management and Owners.
- The Cost of Labor Rates – There are typically many different labor rates depending on the job an employee does or the work experience and time in service.
- The Number of Labor Hours – Labor hours are the hours the die casting machine made parts but sometimes may include hours in inspection, packaging and processing.
- Setup Costs for equipment and die casting molds – There are hours of setup required before a die casting machine can make parts. It takes a few hours to put a die into the die casting machine, it takes a few hours to mount inserts into a mold base, it takes a few hours to melt a bath of metal before production begins.
- Die Casting Metal Amounts – How much die casting metal does each part need? How much was used to produce the part? How much needs to be removed in the clean up process? How much metal was lost and how much can be recovered?
- Die Casting Metal Cost Each Pound – Various die casting metal alloys have a different cost each pound. Some alloys are common and cost less than the more uncommon alloys. If an alloy is used for only one job, there is sometimes a minimum metal lot cost for the bath.
- Value added processes also sometimes known as Outside Process costs – The processes that are required to change the casting from the raw state to a completed part that our customer wants has a cost. Machining costs and coating costs are the more typical value added costs.
These costs are spread through out the production run of hundreds or thousands of diecast parts. When our customer needs only a few parts, they will need to pay a higher cost each die casting part to cover some of the variable and minimum costs.
Another Web Page with Die Casting Part Cost Information:
https://www.kineticdiecasting.com/kdc/optimal-die-casting-production-part-quantity/
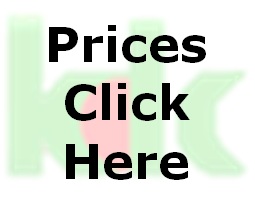
Die Casting Part Prices
Contact Kinetic Die Casting Company to get a die casting part cost or die casting part prices:
Kinetic Die Casting Company
6918 Beck Avenue
North Hollywood, California USA
818-982-9200
sales@kineticdc.com
Die Casting Tooling and Its Importance
Die Casting Tooling and Its Importance. Die casting tooling, otherwise known as dies, are typically prepared from alloy steel. The dies are finished from at least two sections to allow casting elimination. Due to the efficient approach of die casting in some companies, some dies also come in portable slides, with certain sections that can without difficulty drill holes so as to build the ideal shape as demanded by clients from die casters. In the procedure, die casting tooling allows simple production of holes through the predetermined die half. The molten metal is then dispensed into the hole in order to dry in the cavity and manufacture the precise dimensions contoured in the plating. Dies may also have locking pins, which are utilized in order to stick together two halves and to take away the cast part.
Once the die casting machine is put to a close, the two halves are reserved in close contact by the hydraulic pressure inside the equipment. Once this is done, a die casting tooling is fashioned to use as fundamental components for diverse automobiles and construction needs. Aside from the die casting machine being an vital part of the tooling, a die casting trim is also being employed to put off the surplus aluminum which is located around the produced parts. A die casting trim is a critical part of aluminum die casting tooling, as it help diminish the expense brought about by slow production of materials. When this is utilized, the dies are mounted on a trim press so as to aid in bringing together the two die halves.
Kinetic Die Casting manufactures aluminum military parts, aluminum hardware, and aluminum die castings. Visit our website for a quote: Kinetic Die Casting Company
Video of Auto Parts at Kinetic Die Casting Company
Automotive Die Casting Parts from
Kinetic Die Casting Company
Kinetic Die Casting Company makes several auto parts for our customers. This automotive parts video shows a few of the automotive parts we produce for our customers. On our website, we show other pictures of automotive parts. Aftermarket car parts manufacturers depend on companies like Kinetic Die Casting to help with the design of the part and produce auto parts at a competitive price.
Aluminum auto parts in this video are produced from a few parts to thousands of car parts a day. Many features of the automotive part are manufactured “near net shape” to save the cost of wasted materials and the additional labor of machining. Mounting holes are usually produced into the aluminum auto part during production. also saving cost. Many of the primary “tier one” automotive manufacturers have their own manufacturing plants. They also purchase aluminum automotive parts from companies such as Kinetic Die Casting Company.
Contact Kinetic Die Casting Company today if you need an automotive part in aluminum or zinc. We are located just north of Los Angeles, California at 6918 Beck Avenue, North Hollywood 91605.
Call 800-524-8083 or Email at sales@kineticdc.com