U.S. Turbine Blade-Making Plant to Layoff Majority of Work Force Posted: 27 Nov 2009 02:11 PM PST Gamesa (HQ in Spain) blames one of the important reasons many U.S. manufacturers in other industries have too: Banks unwilling to extend credit …
Continue reading
Tag Archives: Die Casting Process
The Die Casting Part Production Process Explained 2019
What is the Die Casting Process? The Die Casting Part Production Process Explained.
Kinetic Die Casting Company uses a manufacturing process called “Die Casting” to make aluminum die casting parts and zinc die casting parts. But, what is the die casting part production process? Here is a GIF image I have on our home page to demonstrate:
demonstration of the die casting process
“Aluminum die casting is an aluminum metal parts production process where molten aluminum metal alloy is injected into a steel die, under extreme pressure, to manufacture aluminum parts” (Substitute the word “zinc” for “aluminum” in zinc die casting part production process)
Another GIF example example is on this web page:
(click) What is Die Casting?
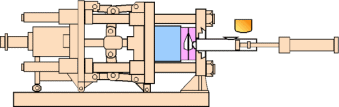
Cold Chamber Die Casting Process
The image pictured above depicts a Cold Chamber Die Casting Machine as it makes parts. The term “Cold Chamber Die Casting” refers to a separate metal melting furnace. The High Pressure Die Casting, cold chamber die casting process follows this sequence:
Look at the die casting machine image above
- The die casting machine opens the die casting mold.
- The prior part is removed and the die cast mold is sprayed for the next part
- The aluminum is poured using a ladle into a shot cylinder
- The shot piston injects the metal into the die casting mold.
- The machine opens and the process starts again.
Contact Kinetic Die Casting Company for more information about the high pressure die casting process and about how to get great die casting parts at a great price and delivered quickly, no matter what quantity you need.
Kinetic Die Casting manufactures aluminum military parts, aluminum hardware, and aluminum die castings. Visit our website for a quote: Kinetic Die Casting Company
Die Casting Process
What is Die Casting?
Aluminum Die Casting Prices
Why Should You Use Die Castings?
Kinetic Die Casting Company
Kinetic Die Casting Company 6918 Beck Avenue, North Hollywood, California 91605 USA
E-mail sales@kineticdc.com Toll Free: (800) 524-8083 Local: (818) 982-9200 Fax: (818) 982-0877
Die Casting Parts Prices
500 Shots Daily
Kinetic Die Casting Company uses a process of making 500 to 1000 aluminum die casting parts every day. Last week, in my multiple cavity die casting tool article, I briefly described the die casting shot cycle as: Die Open, Spray, Die Close, Inject Metal, Open Die, Eject Part and Repeat. This takes about one minute each shot cycle.
- Here are the details of each Step of the die casting production cycle:
- Die Open – The hydraulic system opens the die casting machine platens. The die casting mold is attached to the die platens, opening the die wide so the two halves can be accessed.
- Spray – Molten metal will stick to the steel die if a release agent is not used to coat the tool. The cavities, the slides, the core pins and ejector pins are sprayed also to cool them down.
- Die Close – When the die has been sprayed the machine is closed with hydraulic pressure so the two die halves are closed and sealed together. Sometimes, high pressure nitrogen gas is used to speed the die closing.
- Inject Metal – The metal is poured into the shot sleeve and a piston drives the molten metal into the mold. Hydraulic pressure is used to push the metal into the mold. Higher pressures are applied to push out gasses that cause porosity. High Pressure Nitrogen Gas is used to accelerate the piston faster and to add more pressure to squeeze out gasses.
- Open Die – The die casting machine opens the platens
- Eject Part – The Die casting machines moves a movable platen to push against the ejector plate. The ejector plate pushes the ejector pins. The ejector pins push the part out of the cavity
- – Repeat
In a nutshell, This is the die casting shot cycle. Each shot cycle takes about a minute to complete. We make 500 parts a day with a single cavity die.
Permalink: https://www.kineticdiecasting.com/kdc/500-shots-daily/
“The Parts We Make Today, We Ship Today”
What Are Die Casting Parts?
Die Casting Aluminum Heat Sinks
Aluminum Boxes Die Castings
Aluminum Parts or Plastic Parts
Kinetic Die Casting Company 6918 Beck Avenue, North Hollywood, California 91605 USA
E-mail sales@kineticdc.com Toll Free: (800) 524-8083 Local: (818) 982-9200 Fax: (818) 982-0877
Die Casting Process
Kinetic Die Casting Company uses the die casting process to make aluminum die castings and zinc die casting parts. The die casting process, simplified, is described as follows:
- Our customer provides us tooling (https://www.kineticdiecasting.com/tooling.html), a die, a mold or inserts that we use to make their parts. We can also produce the tooling for our customers.
- We put together the tooling and mount the tooling in our die casting machine. This takes a few hours.
- We fill a furnace with the proper die casting alloy metal (https://www.kineticdiecasting.com/Alloy_Data.pdf) to make the parts for our customer. The metal takes 4 hours to melt to the casting temperature.
- While the furnace is heating up we heat up the tooling to make the castings.
- When the tooling is hot and the furnace has melted the aluminum, we begin the die casting process.
- We spray the tooling with a release agent so the parts do not stick in the tooling.
- We close the tooling inside our die casting machine.
- The metal is ladled into a shot sleeve, a piston drives the metal into the tooling using great force.
- Our die casting machine opens, the ejector pins push the part out of the tooling
- We begin the process again by spraying the tooling.
- We repeat this process 200 times to 500 times in a 10 hour shift.
- When completed making raw castings, we trim the excess material called “flash”. We use a trim die in a trim press or we sand parts with a belt sander and file them by hand. Sometimes this takes longer than the casting process.
- At this point, some parts are put in boxes and shipped the same day. Other parts are machined. Some parts get painted or chemical coated. All parts are inspected prior to shipping to our customers.
This is a very simplified description of the die casting manufacturing process.
“The Parts We Make Today, We Ship Today”
Kineticdc makes:
What is Die Casting
Die Casting Part Pictures
Quote Die Casting Part Prices
Diecast Tooling
Kinetic Die Casting Company 6918 Beck Avenue, North Hollywood, California 91605 USA
E-mail sales@kineticdc.com Toll Free: (800) 524-8083 Local: (818) 982-9200 Fax: (818) 982-0877
Permalink: https://www.kineticdiecasting.com/kdc/die-casting-process/
Porosity in Diecastings
What is Die Casting Porosity? (Die Casting Porosity) In order for you to know what die casting porosity is, you need to know the die casting basics. The most common form of Die Casting Porosity is a kind of factory defect in which die cast parts contain small pockets of void space and air within the metal, causing it to become porous.
Porosity in Die Casting is the air trapped by the metal inside the die casting parts. To know more, a basic knowledge of the die casting process is necessary. Die casting is a process wherein a particular amount of molten metal is put inside a shot cylinder, then it is applied (plunged) with great force with a piston so as to force the metal into a die cast mold or die cast die. During this “plunging process”, air inside the cylinder is forced along with the metal into the die casting mold. It is a very fluid turbulent process. The air forced into the mold with the metal and the metal already inside the mold is forced out of the mold through a series of gates, vents and overflows.
After this, the metal is left to cool down and harden or freeze inside the mold. The metal is then removed as a die cast part. The same process is repeated over again.
Die casting companies use metals which are non-ferrous, or do not contain Iron, as this is the highest factor for oxidation and rusting. Several examples of non-ferrous metals include zinc, aluminum, lead, Magnesium Die Casting, tin and copper. Kinetic Die Casting only uses aluminum die casting and zinc die casting.
In the worst case, die casting parts porosity, weakens die casting parts, if the voids or pockets are very large. Porosity typically matters most in pressure tight die casting parts. When the air escapes through a die casting part, it is typically caused by porosity.
The many forms of Die Casting Porosity are caused by many variables:
- Metal and Mold Temperatures
- Material Cleanliness
- Die Cast Mold Design
- Die Cast Part Design
- Die Casting Machine Pressures
- Die Casting Machine Shot Speed
- Die Casting Spray or Mold Release
- Other forms of porosity can be from “shrinkage” or wall thickness.
Employees of Kinetic Die Casting are POROSITY EXPERTS in die casting parts that need to be free of porosity.
Permalink: https://www.kineticdiecasting.com/kdc/porosity-in-diecastings/
Contact Kinetic Die Casting today if you need “solid” die casting parts.
Kinetic Die Casting, Inc.
6918 Beck Avenue
North Hollywood, California USA 91605
818-982-9200 telephone
818-982-0877 fax
Kinetic Die Casting manufactures custom metal parts to their customer. If you would like more information about Kinetic Die Casting, please visit our website:Kinetic Die Casting Company
NADCA West Coast 2019
NADCA Die Casting Congress West, Date: March 7, 2019, Location: 5757 Telegraph Road, Commerce, CA 90040
The NADCA West Coast 2019 Congress will feature technology highlights from our Congress in Indianapolis, last fall. The event begin with a breakfast followed by a full day of presentations. Presentations to include:
State of the Industry
Presented by Beau Glim, North American Die Casting Association
An update on the current state of the die casting industry.
On Demand Melting
Presented by Charles Monroe, University of Alabama at Birmingham
A look at research into induction melting technology for the die casting process. Such technology has the potential to revolutionize the die casting process by melting only the metal needed to make one shot at a time. This eliminates the energy needed to hold the metal in a liquid state, reduces the chance for contamination of the metal, and provides flexibility to use different alloys. On Demand Melting technology is also being leveraged to research the process of die casting titanium alloys.
Mechanical Properties of Modern Die Castings
Presented by Paul Brancaleon, North American Die Casting Association
NADCA has published data for die casting properties based on typical values taken from tensile bars cut from castings that had the skin removed. This provides property from data that is not always in line with castings made in industry. Current research is collecting more accurate data on different alloys and thicknesses of aluminum die castings.
Advanced Core Design & Manufacturing / Quality Control Technology
Presented by Carl Soderhjelm, Worcester Polytechnic Institute
Advancements in technology are improving the die casting process and the way die castings are inspected. Additive manufacturing allows die casters a way to create conformal cooling channels in cores that previously had insufficient cooling. Further research is being conducted to identify the process and design parameters for additively manufactured cores. Die casting inspection also benefits from technology improvement. One technology that is seeing more use in the die casting industry is computed tomography (CT) scanning. This technology can more accurately detect porosity inside the casting.
Testing of Die Lubricants
Presented by Charles Monroe, University of Alabama at Birmingham
Die lubricants are necessary for the die casting process. They prevent the molten metal from soldering to the die, minimize ejection force, and locally cool the die. But what distinguishes one lubricant from another? Research has been performed to create laboratory tests that can identify characteristics of different lubricants.
Machine Learning in Die Casting
Presented by Beau Glim, North American Die Casting Association
The die casting process is full of data and as the process becomes more automated the data becomes easier to collect. A human, looking at a spreadsheet, can only analyze so much data. To fully understand all of the interacting variables in the die casting process machine learning needs to be utilized.
The cost for each event is just $50 for NADCA Members and $75 for Non-Members (note that registration includes access to breakfast and lunch). In addition, if you will be sending 5 or more people we are offering special pricing.
Die Casting Congress West – March 7, 2019
Information and registration can be found here.
Sign Up Link: www.diecasting.org/store/events/registration.aspx?event=conwest19
If you have any questions please feel free to contact Melisa Ryzner,CMP directly at mryzner@diecasting.org or 847.808.3161.
Permalink: https://www.kineticdiecasting.com/kdc/nadca-west-coast-2019/