For Sale Used DME MUD Base This is a double 12×15 zinc Master Unit Die Holder. Hot Chamber Zinc Double DME style Master Unit Die Holder for sale. These unit die holders are sometimes known as a MUD Base. The …
Continue reading
Tag Archives: Diecasting Process
Zinc Die Casting Tooling Facts in 2020
Zinc Die Casting Tooling Facts. Zinc die casting tooling is a technique to form molten zinc into a shape using molds called dies or die casts. The tooling is the mold utilized in the procedure, and it is largely composed of a cover and ejector. The zinc is melted into molten form and then powerfully emptied into the cover die with the container bearing the wanted pattern. The melted zinc settles on the mold and toughens. Later, it is removed through the ejector. Die casts for zinc can have added features such as trim casts, inserts and multiple cavities reliant on what needs to be formed.
There is a request for
zinc die casting tooling because zinc has plenty of perfect characteristics:
Zinc die cast tooling is made of tough materials to safeguard that the liquefied zinc will be correctly shaped into the anticipated form. There are likely mistakes in die casting such as porosity, uneven zinc distribution, etc. A great zinc die caster will be extremely cautious in following the normal guidelines so that quality zinc items are manufactured.
This is the blog on the Kinetic Die Casting Company web site. We make several types of Aluminum Handle Parts. Look at this website page for more details: www.kineticdiecasting.com/handle.html. Contact Kinetic Die Casting Company at 818-982-9200 or email us at sales@kineticdc.com. Use this webpage to request “die casting part prices” www.kineticdiecasting.com/replyform.html
Die Casting Tooling and Die Casting Molds
Die Casting Tooling Information
Tooling Used in Die Casting
Frequently Asked Die Casting Questions
Die Casting Tile Molds
Kinetic Die Casting Company 6918 Beck Avenue, North Hollywood, California 91605 USA
E-mail sales@kineticdc.com Toll Free: (800) 524-8083 Local: (818) 982-9200 Fax Number
Die Casting Tooling Prices
Machining Aluminum 2020
Aluminum Parts Machining Differs from Steel Parts Machining. Aluminum can be used in many ways. However there are different ways on how you can work with it. Aluminum parts machining requires less power compared to steel parts or cast iron parts because they are light weight.
Aluminum parts machining can be different in cast iron machining. It’s the type of tools and tooling technologies that you will use will make a difference.
Kinetic Die Casting Company makes aluminum die cast parts. If you are working with aluminum parts, the spindle of the machine should be strong and forceful. Spindles require higher speeds along with a lesser low-end torque compared to machining other metals like steel. Also, the spindle should be stiff because it will work in very fast conditions. Other experts on this field recommend the use of HSK tapers to ensure accuracy and rigidity. Moreover, if you are using very fast tools, rotating inertia can be reduced with the use of closed-loop spindles powered by a motor.
Furthermore, it requires little cutting forces if you are working out with aluminum parts. The machine has to be well-damped and stiff.
Since you are working with high speeds, there’s a chance of thermal growth. It can create a major problem if you are working out with light metals. It can lead to a major problem if you are working with light metal parts like aluminum.
Find yourself a machine with thermal control system. A cooling system is recommended in order to reduce the frictional heat in the bearings when the higher spindle speeds up. Also, you must protect the spindle against coolant penetration by sealing it because the entire machining operation of a light metal is not dry.
Kinetic Die Casting manufactures products like aluminum hardware, and aluminum boxes. If you would like more information on Kinetic Die Casting, please visit our website:Kinetic Die Casting Company
Kinetic Die Casting Company 6918 Beck Avenue, North Hollywood, California 91605, United States of America
E-mail sales@kineticdc.com USA Toll Free: (800) 524-8083 Local: (818) 982-9200 Fax: Fax Number
To get prices for Die Casting Tooling Molds or Parts: RFQ Die Casting Part Prices
Kinetic Die Casting Company makes:
FAQ Die Casting Questions and Answers
Kinetic Die Casting Capabilities
Kinetic Die Casting Jobs
Roof Tile Molds Company

Pressure Die Casting Aluminum Military Parts 2020
Pressure Die Casting Aluminum Military Parts vs Sand Casting. The military is an important part of any nation. State of the art technology gives a country a heads up against other possibly invading or threatening army. And with the invention of weapons of mass destruction, powerful nations keep outdoing each other when it comes to military technology.
Mostly, military equipment and weapons are made of sturdy metal. Precision is important, that is why the technology of making military parts is also important.
For aluminum parts, cold chamber pressurized die casting is used. In Pressure Die Casting Aluminum Military Parts vs Sand Casting, surely die casting is the better option. Sand casting is one of the oldest ways of molding heated metal. While this is still a reliable method, its products are not as good as die casting. First, the surface is not as polished. The sizes and parts are also not as accurate as planned. The sand makes the military parts rough in surface. It will need a lot of other processes to make it polished.
With die casting, aluminum parts are sure to be precise in size and parts. Complicated designs are complete, with every crevice and tiny part intact. Sizes will be 99% accurate. This is very important for military parts.
To get a price for aluminum die casting parts or die casting tooling, call toll free 800-524-8083 and ask for sales. Or email us at sales@kineticdc.com for a fast response on a price quote.
Kinetic Die Casting is located in Southern California. KDC specializes in aluminum and zinc die casting tooling. If you would like a quote, please visit our website:Kinetic Die Casting Company
Die Casting Military Parts
Military Die Castings
Die Casting Part Pictures
Military Die Casting Photos
Buy American Die Casting Parts
Kinetic Die Casting Company 6918 Beck Avenue, North Hollywood, California 91605 USA
E-mail sales@kineticdc.com Toll Free: (800) 524-8083 Local: (818) 982-9200 Fax: (818) 982-0877
Die Casting Military Parts Prices
Die Casting Fixtures 2020
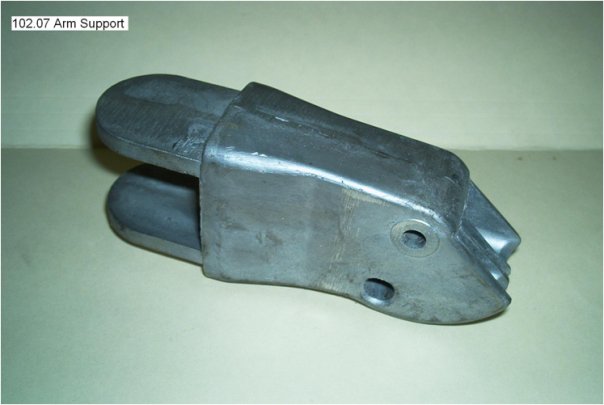
Die Casting Lighting Fixtures
The main purpose of lighting fixtures or parts is to create artificial light. A lighting fixture consist of 0 parts—the light source, light reflector that directs the light to a certain point, an opening (with lens or without lenses), the light housing for protection, an electrical counterweight, and a cord connecting to the power source. Lighting fixtures can be classified as indoor lighting fixtures and outdoor lighting fixtures.
Before the introduction to an aluminum die casting company, lighting parts are made by welding pieces together. This process is costly, time consuming, and labor extensive. Nowadays, lighting parts are manufactured by die casting, a process wherein molten metal is forced into mold cavities. Die casting is beneficial if you are producing large quantities of small to medium sized lighting parts with good details,
Aluminum is lightweight and sturdy, a material often used to make lighting parts because of its durability and good thermal and electrical properties. Die cast aluminum lighting parts are made faster because they can be produced in net shape, meaning there are no welding or drilling methods needed after. Holes can be added to the mold cavities. These holes are necessary for the installation of covers or lids.
Die cast aluminum lighting parts are used in medical offices and parking garages for lighting fixtures. They are also used for bullet lighting fixtures, street traffic lights, outdoor and wall lighting fixtures. Furthermore, there are special light parts made for Aluminum lighting fixtures used for automobile lighting, marine lighting, medical lighting, and aerospace lighting.