How are Aluminum Speaker Parts made? Making aluminum speakers needs the proper tools and materials to be used. But this article will only give you the brief idea on the basic steps in making aluminum speaker parts. So how are …
Continue reading
Tag Archives: Diecasting Process
Cast Parts 2020
Cast-Parts is an American die casting company located in California, USA. Cast-Parts produces aluminum diecast parts and zinc diecast parts using a process called “High Pressure Die Casting Process”. The high pressure die casting process is where a molten metal alloy is injected using high pressure into a die casting mold or diecasting die to make metal diecast parts.
This die casting process is enabled by the use of high pressure die casting machines. The Die Casting Machines that Cast-Parts uses are computer-aided production controled to produce and ship cast parts to our customers on time. We will usually ship quality products in four weeks from the time the order is placed. We can expedite some cast part shipments in less than two weeks.
Our cast parts die casting machines range up to 650 tons to make parts in aluminum die casting parts from .001 pounds to 5 pounds. Our zinc die casting parts range from less than an ounce to over a few pounds. We make many types of die cast parts from less than an ounce up to a ten pound shot.
To comment please email Cast-Parts sales@Cast-Parts.com.
Cast Parts Die Casting Company
Die Casting Parts Process
Die Casting Part Types
American Die Casting Company USA California
Die Casting Tooling Prices Request
Die Casting Tooling
Die Casting Part Prices and Cast Parts Contact Page
Die Casting Alloys for High Pressure Die Casting
Site Map Page for Cast Parts Die Casting Company
Links for Cast Parts Resources listings
Die Castings Blog for Cast Parts Die Casting Company
For Large Industries: The Process of High Pressure Die Casting
For Large Scale Industries: The Process of High Pressure Die Casting. The process of high pressure die casting is popular among large scale production lines. It is considered as one of the most cost effective and fastest metal working process, when compared to forging, sand casting and other types of machining. Traditional die casting is also called high pressure die casting because the molten metal is forced into the mold cavity by using high pressure.
The mold cavity is formed by two halves. They are the cover die and the ejector die. The section where the two halves meet is called the parting line. During casting, molten metal is injected between the dies. The metal is allowed to flow through an opening in the cover die half. High pressure, between 10 to 175 mPa, is maintained until the molten metal solidifies. This process of high pressure die casting ensures uniform solidification of the final product. Hence, it produces uniform work pieces with high yield strength. There are two types of the method: cold chamber and hot chamber casting. The choice depends on the melting point of the metal. For example, zinc and aluminum alloys can only be processed in cold-chamber environments.
The process of high pressure die casting has many applications, ranging from the toy industry to automotive and computers. The technique also minimizes, if not totally eliminates, post-machining like sanding or grinding. Therefore, there are less post-production costs. However, this technique is only recommended for large scale businesses. The initial cost of construction of dies, due to painstaking details and strength, is relatively higher than other machining processes.
To get a price for aluminum die casting parts or die casting tooling, call toll free 800-524-8083 and ask for sales. Or email us at E-mail sales@kineticdc.com for a fast response on a price quote.

Kinetic Die Casting manufactures aluminum die castings creating aluminum die casting boxes, aluminum handle hardware, and aerospace die casting. If you would like to get a quote, please visit our website: Kinetic Die Casting Company
Kinetic Die Casting manufactures products like heatsink die casting, aluminum housings, and lighting fixtures. If you would like more information, please visit our website:Kinetic Die Casting Company
Die Casting Process
What is Die Casting?
Aluminum Die Casting Prices
Why Should You Use Die Castings?
Kinetic Die Casting Company
Kinetic Die Casting Company 6918 Beck Avenue, North Hollywood, California 91605 USA
E-mail sales@kineticdc.com Toll Free: (800) 524-8083 Local: (818) 982-9200 Fax: (818) 982-0877
Die Casting Parts Prices
Die Casting Tooling 2020
Die Casting Tooling. Die casting is a modernization that makes it possible to mass production for manufacturers. It is the procedure of forcing molten metal under high pressure into reusable steel molds. These molds are otherwise dubbed dies. It creates multifaceted shapes with high degree of correctness and repeat-ability.
A die casting tooling is employed for high volume of production and is typically a class “A” complete die. It comes in a variety of sizes and shapes. It is frequently made from steel and often weighs several hundred pounds for a complete mold.
A die casting tooling is utilized to produce a part in a die casting machine. Surfeit aluminium from a die casting tooling is manufactured by a die casting trim, saving as much as 15% in the part price by speeding up the manufacture procedure.
Die casting dies, die casting molds and insert die are also known as die casting tooling. It comes either with single cavity or numerous cavities. If the cavity is soft, it can be damaged and wore off from erosion. It generally needs particular understanding on how to mold tooling for aluminium.
To expand its tooling life, die casting tooling needs heat treatment. Getting a prototype to test and produce a design is prudent because it’s reasonably priced and takes less time to construct. Nevertheless, once damaged, a prototype cannot be customized.
Die casting tooling is a requirement in the manufacturing industry. To get a longer life for the molds, be sure to obtain only from toolmakers that utilizes enough steel. The cost differs for trim dies and cavity inserts.
Kinetic Die Casting manufactures aluminum die castings creating aluminum die casting boxes, aluminum handle hardware, and aerospace die casting. If you would like to get a quote, please visit our website: Kinetic Die Casting Company
Die Casting Tooling and Die Casting Molds
Die Casting Tooling Information
Tooling Used in Die Casting
Frequently Asked Die Casting Questions
Die Casting Tile Molds
Kinetic Die Casting Company 6918 Beck Avenue, North Hollywood, California 91605 USA
E-mail sales@kineticdc.com Toll Free: (800) 524-8083 Local: (818) 982-9200 Fax: (818) 982-0877
Die Casting Tooling Prices
The Die Casting Part Production Process Explained 2019
What is the Die Casting Process? The Die Casting Part Production Process Explained.
Kinetic Die Casting Company uses a manufacturing process called “Die Casting” to make aluminum die casting parts and zinc die casting parts. But, what is the die casting part production process? Here is a GIF image I have on our home page to demonstrate:
demonstration of the die casting process
“Aluminum die casting is an aluminum metal parts production process where molten aluminum metal alloy is injected into a steel die, under extreme pressure, to manufacture aluminum parts” (Substitute the word “zinc” for “aluminum” in zinc die casting part production process)
Another GIF example example is on this web page:
(click) What is Die Casting?
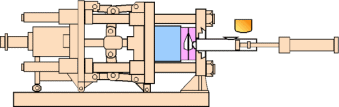
Cold Chamber Die Casting Process
The image pictured above depicts a Cold Chamber Die Casting Machine as it makes parts. The term “Cold Chamber Die Casting” refers to a separate metal melting furnace. The High Pressure Die Casting, cold chamber die casting process follows this sequence:
Look at the die casting machine image above
- The die casting machine opens the die casting mold.
- The prior part is removed and the die cast mold is sprayed for the next part
- The aluminum is poured using a ladle into a shot cylinder
- The shot piston injects the metal into the die casting mold.
- The machine opens and the process starts again.
Contact Kinetic Die Casting Company for more information about the high pressure die casting process and about how to get great die casting parts at a great price and delivered quickly, no matter what quantity you need.
Kinetic Die Casting manufactures aluminum military parts, aluminum hardware, and aluminum die castings. Visit our website for a quote: Kinetic Die Casting Company
Die Casting Process
What is Die Casting?
Aluminum Die Casting Prices
Why Should You Use Die Castings?
Kinetic Die Casting Company
Kinetic Die Casting Company 6918 Beck Avenue, North Hollywood, California 91605 USA
E-mail sales@kineticdc.com Toll Free: (800) 524-8083 Local: (818) 982-9200 Fax: (818) 982-0877
Die Casting Parts Prices
Three of the Most Popular Die Casting Alloys 2019
Three of the Most Popular Die Casting Alloys. Aluminum is the most accepted out of all die casting alloys. Besides its lightweight features and its sturdy ability, aluminum is also found to be very inexpensive measured up to other die casting alloys. When choosing the ideal material to utilize in die casting, it is vital to have concise information as to how each alloy is different from one another. Although aluminum may have a lot of benefits and advantages compared to other materials, some die casting companies also prefer not to use aluminum owing to its high shrinkage capability and also its receptivity to high temperature.
Copper is one of the various other die casting alloys like zinc die casting available in the scientific procedure. One of the advantages of employ copper is its inflexibility and its ability to decrease ductility. Copper is also identified not be receptacle to corrosion, generating an outstanding substitute to aluminum. On the other hand, if you are looking for a type of alloy that is able to work on narrower walls compared to the effectiveness of aluminum, you can also use Zinc as an alternative. Zinc has the capability to close tolerances because of its fluidic nature that is highly influenced by high temperatures. When die casters decided Zinc as its die casting alloy, the casting is processed at a lower temperature than usual so as not to completely melt the die. As soon as the die is shaped, it is much easier for die casters to permit the result to solidify due to the material’s sensitivity towards temperature.
Die Casting Alloys
Die Casting Alloys
Die Casting Metals and Technical Terms
Die Casting Technical Information
Die Casting Aluminum Parts
Die Casting Zinc Parts
Kinetic Die Casting Company 6918 Beck Avenue, North Hollywood, California 91605 USA
E-mail sales@kineticdc.com Toll Free: (800) 524-8083 Local: (818) 982-9200 Fax: (818) 982-0877
Die Casting Parts Prices