Today is Friday, February 2nd, 2019 “Groundhog Day 2019” This holiday is celebrated as a fun way to predict the coming winter weather. This day is celebrated each year on February 2nd. Groundhog Day was a traditional day used to …
Continue reading
Tag Archives: Diecasting Process
Different Forms of Die Casting Tooling
Different Forms of Die Casting Tooling. Die casting tooling can also be dubbed insert die, die casting molds, or die casting dies. They can come in a variety of forms, styles, and sizes. One of the shapes of die casting tooling is the die cast tooling inserts. They are the least pricey among the tooling that needs heat-treating so that the life of the insert will be extended. The tooling life is the number of parts probable to be completed in the inserts. The other form is the Prototype die casting tooling insert. They are the same with the first form of tooling but the only dissimilarity is that this type require not be heat-treated and can be broken easily.
The next type is die casting unit die tooling and this is smaller than the total mold but better than the inserts. It also uses more steel compared to the inserts and less steel than the complete mold.
Complete Class A die casting die fits into the die casting machine without the use of any base or holder. This type creates better quality parts and more die life. It has waterlines and trim dies that can speed up the manufacturing.
Die casting Family Mold tooling has several cavity die inserts that can process single or multiple parts each cycle. It should be detached from the machine when changing inserts so it is expensive and not time proficient.
Trim dies can save time in production and cut the surplus alloy in the parts shaped. They are mounted into a trim press and are pressed together with tons of pressure.
Kinetic Die Casting can manufacture aluminum automobile parts, heat sinks, aerospace parts and much more. If you are looking for aluminum or zinc parts, visit our website Kinetic Die Casting Company
Die Casting Part Prices
Kinetic Die Casting Company discusses how Die Casting Part Prices are determined. A die casting company is sometimes also known as a Job Shop Manufacturer. In other words, the die casting company provides metal products to other manufacturing companies. These other manufacturing companies, sometimes are OEMs (Original Equipment Manufacturers). These die casting metal products, die castings, are used in the product produced by the OEM customer, who is always a manufacturing company.
Die casting part prices or diecastings prices are determined using only a few factors.
- Utilities Costs (Water, Gas and Electric)
- Overhead and Fixed Costs
- The Cost of Labor Rates
- The Number of Labor Hours
- Setup Costs for equipment and die casting molds
- Die Casting Metal Amounts
- Die Casting Metal Cost Each Pound
- Value Added Processes.
All of these variables listed to manufacture die casting parts. Typically die castings cost less than $1.00 to $5.00 each die casting part.
- Utilities Costs – Are used to melt the die casting metal for two or four hours prior to die casting production. The high pressure die casting machines use a lot of electricity to operate the high pressure pumps.
- Overhead and Fixed Costs – These are costs that are frequently overlooked, such as Rent, Insurance, Medical Benefits and Salaries for Management and Owners.
- The Cost of Labor Rates – There are typically many different labor rates depending on the job an employee does or the work experience and time in service.
- The Number of Labor Hours – Labor hours are the hours the die casting machine made parts but sometimes may include hours in inspection, packaging and processing.
- Setup Costs for equipment and die casting molds – There are hours of setup required before a die casting machine can make parts. It takes a few hours to put a die into the die casting machine, it takes a few hours to mount inserts into a mold base, it takes a few hours to melt a bath of metal before production begins.
- Die Casting Metal Amounts – How much die casting metal does each part need? How much was used to produce the part? How much needs to be removed in the clean up process? How much metal was lost and how much can be recovered?
- Die Casting Metal Cost Each Pound – Various die casting metal alloys have a different cost each pound. Some alloys are common and cost less than the more uncommon alloys. If an alloy is used for only one job, there is sometimes a minimum metal lot cost for the bath.
- Value added processes also sometimes known as Outside Process costs – The processes that are required to change the casting from the raw state to a completed part that our customer wants has a cost. Machining costs and coating costs are the more typical value added costs.
These costs are spread through out the production run of hundreds or thousands of diecast parts. When our customer needs only a few parts, they will need to pay a higher cost each die casting part to cover some of the variable and minimum costs.
Another Web Page with Die Casting Part Cost Information:
https://www.kineticdiecasting.com/kdc/optimal-die-casting-production-part-quantity/
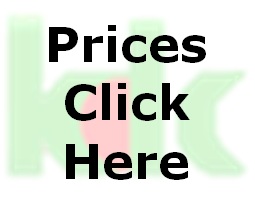
Die Casting Part Prices
Contact Kinetic Die Casting Company to get a die casting part cost or die casting part prices:
Kinetic Die Casting Company
6918 Beck Avenue
North Hollywood, California USA
818-982-9200
sales@kineticdc.com
What People Don’t Know About Die Casting Tooling
What People Don’t Know About Die Casting Tooling. Aluminum Lighting Fixtures use die casting tooling. Tooling is also known as insert die or casting molds which may come in several different sizes and styles. It is the forming of tools via die casts. It may cost from hundreds of dollars up to thousands depending on the size of the total die cast package. The least costly type of die cast tooling is the die cast inserts. These high pressure die cast inserts are collected basically of the minimum amount of steel essential to manufacture the cavities with a tad bit extra in order to have some allowance for temperature fluctuations. At times nevertheless, this may be hard to achieve as the right density is necessary. If it is too hard, the steel will break due to the high temperature, if the cavities are too yielding, they will wear away rapidly from the molten metal.
In order to first test out the weight and worth of the tool without placing much cost in making an genuine die cast tool, one is suggested to create a prototype die casting tooling insert. This relates in comparable ways to the die cast tooling not including that cheaper metals are utilized and are not heat treated to reduce costs. This is chiefly done to test a design. Clearly it has numerous downsides such as the reduced durability of the tool.
As shown above, there are numerous ways to save hundreds of dollars in die casting tooling. In taking into account the size, assuring the right density of the cavities and by first producing a prototype to test the design before mass producing the die casts, much money can be collected.
Kinetic Die Casting Company can manufacture aluminum car parts, aluminum hardware, and Aluminum Lighting Parts 818-982-9200
http://www.youtube.com/user/kineticdc
Die Casting Tooling KDC
Die Casting Tooling at KDC. Die cast tooling is fondly identified as die casting dies, insert die, or die casting molds by some people. This is obtainable in broad variety of sizes, styles, as well as values. In addition, die casting tooling is made available in single cavities with a single part per cycle while sometimes it comes in several cavities that surrounds more than one part in ever cycle.
Most of the time, companies operating on this procedure would simply create uses of molds for aluminum die cast parts or cold chamber die casting machine tooling dies. The cost may differ, sometimes it comes in a few hundred dollars particularly when making trim dies then it may cost a few thousand for the case of cavity inserts or it may range to numerous thousand dollars for the huge part whole die cast die package.
Additionally, Kinetic Die Casting Tooling is accessible in a plethora of types which encompass of Prototype Die Cast Tooling Inserts, Die Cast Tooling Inserts, Unit die Tooling, Trim Dies for Die Cast Parts, Die Cast Family Mold Tooling, and Complete Class “A” Die Cast Die or else recognized as Mold Tooling. If you are looking for the cheapest type of die casting tooling, choose for die cast tooling inserts. This kind requires heat treating in order to proficiently extend the tooling life. Just in case when the cavity inserts seems to be too hard, there is a propensity that they will not pass the tremendous temperature of the molten metal therefore leading to the crack of steel.
Kinetic Die Casting manufactures a lot of aluminum rooftile plates , trim tile molds, and military die casting.
If you would like a quote, please visit our website: Kinetic Die Casting Company 800-524-8083 or sales@kineticdc.com
http://www.youtube.com/user/kineticdc
Brackets using Die Casting Tooling
Die Casting Tooling is used to make aluminum handles and aluminum brackets. One of the most adaptable processes for producing metal parts that are engineered to precision, die casting is a technique by which molten metal is inserted into steel molds at very high pressures. These molds, referred to as “dies”, have been shaped to mold material into an assortment of complex shapes and tiny parts that display exact correctness and consistency. These metal parts are a creation of greater die casting tooling, and have textured surfaces or flat surfaces depending on their use. Manufactured die cast parts are utilized for a huge number of practical items from aircraft components to brackets and handles.
Using die casting tooling, a high volume of items can be bulk-produced. This is of enormous significance to the metal manufacturing industry, as it enables them to meet a superior demand for specifically-shaped materials made of diverse kinds of metals. Die casting tooling assembly lines power-driven by machines generate a excellent number of metal components and parts that consumers utilize everyday, from aircraft and automobiles, to aluminum handles and aluminum brackets. These die cast parts can range from uncomplicated faucet sinks to complex connector housings.
In die casting, the designer of the die casting tooling employed will want to generate these parts with a mind to matching both the function of these parts, with the speed, cost and quality implicated in the die casting procedure. This comprises the price and possessions of the material to be cast, the operating costs and abilities of the casting machines, and other post-processing procedures such as machine tooling.
Kinetic Die Casting manufactures aluminum and zinc die casting parts. Samples of KDC’s work include die cast speaker parts, aluminum tile plates, and other die cast metal parts. If you would like to have a quote please visit our website: Kinetic Die Casting Company
http://www.youtube.com/user/kineticdc