Secure Mounting for Electronics. Electronic items are usually very fragile and require only a single fall before being permanently damaged like aluminum guitar amplifiers. Another problem is that many of these items are usually mounted onto walls to save space …
Continue reading
Tag Archives: Diecasting Process
How Trim Dies Save Money on Die Casting Parts
How Can Trim Dies Save Me Money on Die Casting Parts? – Is a question, I get asked frequently from potential customers and current customers.
I will discuss what a die casting part trim die is and what it does, but first we need to know a little about how die casting parts are made. The Die Casting Trim Die is part of the die casting part tooling package.
- Die Casting is a manufacturing process where a company melts metal, typically aluminum or zinc, and then injects that metal into a die or mold using extreme pressure.
The molten metal is under so much pressure that the metal “flashes” out around the edges of the part inside the die casting mold. This excess metal is also called “flash”. This flash is typically very thin, sometimes paper thin, wall of metal. The flash is frequently sharp and can cut fingers if not handled carefully. After the part cools sufficiently, the flash must be removed before we can ship the die cast part to our customer.
- The most common ways to remove flash are:
- Using a file or sander – Somewhat labor intensive and subject to “artistic interpretation” from the worker. Not always consistent in the process.
- Using a trim die – A trim die cuts consistently .005″ to .010″ close to edge of the die casting part like a cookie cutter. Is also the fastest way to remove flash.
The trim die is in two parts and each half is bolted on either the upper or lower platen of a trim press. The trim press has typically 15 to 20 tons of closing pressure. The press raises and lowers as the worker actuates the buttons. The die casting part fits perfectly in the trim die bottom, the trim die top half closes on the part and uses a cutting edge to cut the excess metal (flash) away from the part.
Because the trim die cuts the flash from the part accurately and consistently, the part quality is always better when a trim die is used to remove the a flash. So, less money is wasted on poor part quality. The trim press also operates faster than the die casting machine so the flash removal takes less time and labor, thus saving money in part production.
Each of our die casting production cells at Kinetic Die Casting Company has at least one trim press to accommodate a trim die for every die casting production part order. Every customer who owns a trim die, saves money on their part price. Call us today for a FREE competitive part price proposal to make your parts 818-982-9200.
Die Casting Company Makes Aluminum a Perfect Choice
Die Casting Company Makes Aluminum a Perfect Choice. Every die casting company clearly makes it a point to highlight the advantages of aluminum. That is why it has become the ideal choice for the commerce in this time and age. Why is that so? Just picture if the car itself is created of iron parts. Do you believe the cargo carriers will be able to transfer a bunch of cars without any problems at all? The answer to everything is essentially easy. The aluminum is one of the very few lightest metals recognized in the world.
For an automobile company, casting the aluminum offers a decrease in the weight of the whole car. This is the reason which has smoothed the way for the substitution of the iron parts. The same holds true for both the convey and aerospace business. The casting of the melted aluminum alloys into the metal molds is also very economical. They are likewise too practical to use for any die casting company processes. Apply gravity, high pressure, or low pressure die casting and you will still come up with the best finished surfaces and close tolerance. The metal is not hard to shape which thus prevents too much application of machining.
The die casting companies in Australia and the United States are all sticking to one common thought and that is to utilize the use of the aluminum alloys to attain the best finishing products! After all, who doesn’t desire to save much on time, effort, and cost for the whole production procedure?
Kinetic Die Casting manufactures aluminum and zinc die casting parts. Samples of KDC’s work include die cast speaker parts, aluminum tile plates, and other die cast metal parts. If you would like to have a quote please visit our website: Kinetic Die Casting Company
NADCA – North American Die Casting Association
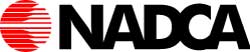
Kinetic Die Casting Company is a corporate member of the North American Die Casting Association NADCA. We have been corporate members for a very long time. The North American Die Casting Association (NADCA) is the sole trade and technical association of the die casting industry. NADCA membership consists of both corporate and individual members from over 950 companies located in every geographic region of the U.S.
These companies include custom die casters (who produce die castings for sale to others), captive die casters (who produce castings for their own use in manufacturing a product), and suppliers to the die casting industry. NADCA members can be found in every type of community across the nation, representing both rural and urban interests.
The North American Die Casting Association (NADCA) represents the voice of the die casting industry. NADCA is committed to promoting industry awareness, domestic growth in the global marketplace and member exposure. Headquartered in Wheeling, IL, the association is comprised of both individual members and corporate members located throughout United States, Canada and Mexico.
The North American Die Casting Association (NADCA) also has an extensive government relations program based in Washington D.C. The program provides government affairs services to NADCA members. NADCA relies on the services of Waterman & Associates to act as the ears, eyes and voice of the die casting industry at the federal level.

The Basics of Die Casting Alloys
The Basics of Die Casting Alloys. Die-casting is very comparable to permanent mold casting, only that the metal which is pushed into the mold experiences higher pressures which total to 10-210Mpa (1,450-30,500) psi. Because of this, the exterior of the die-cast is very fine; the dimensions are also much more precise at 0.2% of casting dimension.
Die-casting may be done in two different ways, either utilizing a cold chamber method or by employing a hot chamber procedure. Both vary in the time exposure of the melt which certain metals need either more or less. Cold chamber procedures are typically utilized for aluminum and copper, also counting its fellow die casting alloys. The metal is located in the cold chamber for each shot and requires less time exposure of the melt. Hot chamber methods normally are utilized for metals that have low melting points and high fluidity. This includes zinc, tin and lead. The die cavity is located permanently in the melted metal. The inlet port of the pressurizing cylinder is exposed as the plunger moves to its opening position. This permits a different charge of melted metal to fill the cavity.
Aluminum, Zinc and Copper are the die casting alloys that are chiefly utilized in die-casting for a variety of reasons. Die-castings are restricted from 20kg to a maximum that is reliant on the metal. Large castings typically have superior porosity problems because of the trapped air and the premature hardening of the die-cast cavity. In essence, many things must considered when performing die-casts in order to make certain the excellence of the metals. Die casting alloys guarantee excellent quality and a great finish.
Kinetic Die Casting is located in North Hollywood,California. KDC specializes in manufacturing zinc and aluminum alloy casting parts. If you would like a quote, please visit our website:Kinetic Die Casting Company
Die Casting Alloys
Die Casting Alloys. A die casting is a method engaged by the metalworking industry to produce and construct metal parts that are good die casting. It is a way of pushing melted metal into reusable molds under high pressure. Flexible alloys are utilized to manufacture a die. The most frequent die casting alloys are zinc, aluminium, magnesium, copper, lead and tin.
Die casting alloys are selected depending on the rewards they have to recommend to manufacturers. Here is how ordinary die casting alloys are distinguished:
There are other die casting alloys apart from the aforementioned. Picking the correct alloy to utilize will seriously depend on its features.
Kinetic Die Casting is located in Southern California. KDC specializes in aluminum and zinc die casting tooling. If you would like a quote, please visit our website:Kinetic Die Casting Company