Heat dissipation is the job aluminum heat sinks perform. Heatsinks are normally used in locations where heat needs to be dissipated such as in hydraulics and more typically in electronics applications. In hydraulic applications, heatsinks use air cooling or water …
Continue reading
Tag Archives: #DieCastingCompany
Taking Flight with Precision Die Casting
Aerospace engineering places a premium on lightweight solutions without compromising strength and durability. Die casting, with its ability to produce complex shapes and intricate features using lightweight alloys such as aluminum and magnesium, offers an ideal solution for manufacturing airplane parts. By leveraging die casting techniques, engineers can design and fabricate components that reduce overall aircraft weight, leading to improved fuel efficiency, increased payload capacity, and enhanced performance. The heart of any aircraft, the engine relies on a multitude of precision-engineered components to generate thrust efficiently and reliably. From turbine blades and compressor housings to engine mounts and heat exchangers, die casting plays a vital role in the production of these critical parts. By harnessing the precision and repeatability of die casting processes, aerospace manufacturers can produce engine components that meet the exacting standards of performance, reliability, and safety demanded by the industry. Aerospace structures must withstand immense forces and stresses during flight, requiring components of exceptional structural integrity and reliability. Die casting enables the production of parts with uniform grain structure and minimal porosity, resulting in enhanced mechanical properties and fatigue resistance. Whether it’s fuselage components, wing brackets, or landing gear assemblies, die-cast parts contribute to the overall strength and durability of aircraft structures, ensuring the safety and longevity of flights.
When precision and reliability are paramount, die casting offers a versatile solution for producing intricate housings, enclosures, and heat sinks. These components provide crucial protection and thermal management for sensitive electronic systems onboard aircraft, ensuring optimal performance and longevity in demanding aerospace environments. By leveraging die casting techniques, manufacturers can achieve the tight tolerances and intricate geometries required for advanced avionics applications. As aerospace technology continues to evolve, so too does the role of die casting in shaping the future of flight. Manufacturers and engineers collaborate to push the boundaries of innovation, leveraging advanced materials, design optimization techniques, and cutting-edge manufacturing processes to meet the evolving needs of the aerospace industry. From additive manufacturing and simulation-driven design to digital twin technology and integrated supply chain solutions, the aerospace die casting sector remains at the forefront of innovation, driving progress and shaping the next generation of aircraft systems and components.
“The Parts We Make Today, We Ship Today”
Kinetic Die Casting Company. Inc.
6918 Beck Avenue, North Hollywood,
California 91605, United States of America
E-mail sales@kineticdc.com
USA Toll Free: (800) 524-8083 Local: (818) 982-9200
Get prices for Die Casting Tooling Molds or Parts:
Quote Die Casting Aerospace Part Prices
Kinetic Die Casting Company makes:
Aerospace Die Casting Parts
Light Fixture Die Casting Parts
Zinc Die Cast Knobs
Zinc die-cast knobs are essential components in various industries, offering durability, versatility, and aesthetic appeal. With excellent strength and corrosion resistance properties, zinc die-cast knobs have become a popular choice for manufacturers due to their ability to withstand both indoor and outdoor applications. This article will delve deeper into the characteristics, benefits, applications, and considerations of zinc die-cast knobs in the manufacturing sector.
Zinc die-cast knobs are manufactured through a process called die casting, which involves injecting molten zinc into a steel mold cavity under high pressure. This process allows for the production of intricate and precise designs, making zinc die-cast knobs a versatile option for various applications. The use of zinc as a base material also contributes to the knobs’ strength and resistance to wear and tear, ensuring a long lifespan even in demanding environments.
One of the key advantages of zinc die-cast knobs is their aesthetic appeal. The material can be easily plated or coated with various finishes, including chrome, nickel, or powder coating, to match different design requirements. This versatility in finishing options allows manufacturers to tailor the appearance of zinc die-cast knobs to suit a wide range of products, from industrial machinery to consumer electronics.
In addition to their visual appeal, zinc die-cast knobs offer excellent tactile feedback and ergonomic functionality. The knobs can be designed with different shapes, sizes, and textures to provide users with a comfortable grip and precise control. This makes zinc die-cast knobs ideal for applications where precise adjustment or manipulation is required, such as in instrumentation panels, control systems, or consumer appliances.
Another significant benefit of zinc die-cast knobs is their cost-effectiveness. The die-casting process allows for high production volumes at a relatively low cost per unit, making zinc die-cast knobs a cost-efficient solution for manufacturers looking to scale up their production. Furthermore, the durability and longevity of zinc die-cast knobs reduce maintenance and replacement costs, providing long-term value for businesses.
Zinc die-cast knobs find wide applications across various industries, including automotive, electronics, furniture, and machinery. In the automotive sector, zinc die-cast knobs are used in dashboard controls, door handles, and HVAC systems, providing drivers with reliable and durable components. In the electronics industry, zinc die-cast knobs are commonly found in audio equipment, home appliances, and industrial machinery, where precision and durability are paramount. When considering zinc die-cast knobs for a specific application, manufacturers should take into account factors such as operating environment, load requirements, and aesthetic considerations. It is essential to work closely with experienced design engineers and material specialists to ensure that the chosen zinc die-cast knobs meet the desired performance criteria and quality standards.
“The Parts We Make Today, We Ship Today”
Kinetic Die Casting Company. Inc.
6918 Beck Avenue, North Hollywood,
California 91605, United States of America
E-mail sales@kineticdc.com
USA Toll Free: (800) 524-8083 Local: (818) 982-9200
To get prices for Die Casting Tooling Molds or Parts:
RFQ Die Casting Tooling Part Prices
Kinetic Die Casting Company makes:
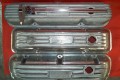
Die Casting Bracket Hardware
Airplane Die Casting Parts
Permalink: https://www.kineticdiecasting.com/kdc/zinc-die-cast-knobs/
Wishing You a Merry Christmas 2024 from Kinetic Die Casting Company
We will be closed from Friday 12/20/24 until Monday 01/06/25.
Celebrating Joy and Unity as the holiday season approaches, Kinetic Die Casting Company extends warm wishes to our valued customers, partners, employees, and friends.
Christmas is a time of joy, reflection, and celebration—a time to come together with loved ones, exchange gifts, and create cherished memories. From our family to yours, we wish you a Merry Christmas filled with laughter, love, and blessings.
Christmas is a time to embrace the spirit of giving and generosity, as we extend kindness and compassion to those around us. At Kinetic Die Casting Company, we are grateful for the opportunity to give back to our community and support those in need during the holiday season. Through charitable initiatives, volunteer efforts, and acts of kindness, we strive to make a positive impact and spread joy to those who may be less fortunate. As we gather with loved ones to celebrate Christmas, we take a moment to reflect on the blessings of the past year and express gratitude for the relationships, opportunities, and achievements that have enriched our lives. We are grateful for the unwavering support of our customers, whose trust and loyalty inspire us to continually strive for excellence in everything we do. We are thankful for the dedication and hard work of our employees, whose commitment and professionalism drive the success of our company. And we are appreciative of the partnerships and friendships that have strengthened our business and enriched our lives.
Christmas is a time to spread joy and cheer, as we embrace the festive spirit and share laughter and happiness with those around us. Whether gathered around the Christmas tree with family, exchanging gifts with friends, or enjoying the sights and sounds of the season, we hope this Christmas brings you moments of pure joy and delight. May the spirit of Christmas fill your heart with warmth and your home with love, as you create cherished memories that will last a lifetime.
As we bid farewell to another year and look ahead to the opportunities that await us in the new year, we do so with optimism, hope, and excitement. The holiday season reminds us of the importance of faith, resilience, and community, as we come together to celebrate the blessings of the past and embrace the promise of the future. As we embark on the journey ahead, we do so with gratitude in our hearts and a renewed sense of purpose, knowing that together, we can overcome any challenge and achieve great things.

Almond Roca Candy
On behalf of Kinetic Die Casting Company, we wish you and your loved ones a Merry Christmas filled with joy, laughter, and blessings. May this holiday season bring you peace, happiness, and cherished moments with those you hold dear. Thank you for your continued support, partnership, and trust. Here’s to a bright and prosperous New Year ahead!
“The Parts We Make Today, We Ship Today”
Kinetic Die Casting Company. Inc.
6918 Beck Avenue, North Hollywood,
California 91605, United States of America
E-mail sales@kineticdc.com
USA Toll Free: (800) 524-8083 Local: (818) 982-9200
Empowering Electronics
Die Casting Enclosure Parts is enabling the creation of high-quality, reliable enclosures that meet the demanding requirements of modern electronics. Let’s delve into the significance of die casting in enclosure parts production and its transformative impact on the electronics industry. Enclosures serve as the first line of defense for electronic devices, shielding sensitive components from moisture, dust, vibration, and electromagnetic interference. Die casting enables the production of enclosure parts with precise dimensions, tight tolerances, and complex geometries, ensuring a perfect fit and maximum protection for electronic assemblies. Whether it’s housing for circuit boards, connectors, or displays, die-cast enclosure parts provide the structural integrity and precision engineering necessary to safeguard critical components and ensure optimal performance in demanding environments.
Heat dissipation is a critical consideration in electronic device design, as excessive heat can degrade performance, reduce component lifespan, and even cause catastrophic failure. Die casting enables the creation of enclosure parts with intricate fin structures, heat sinks, and thermal management features that facilitate efficient heat dissipation and thermal conductivity. By utilizing materials with high thermal conductivity, such as aluminum, die-cast enclosure parts help dissipate heat away from electronic components, ensuring optimal operating temperatures and prolonging the lifespan of sensitive devices.
In addition to protection and thermal management, enclosure design plays a significant role in the functionality and aesthetics of electronic devices. Die casting offers unparalleled design flexibility and customization options, allowing for the creation of enclosure parts with unique shapes, sizes, and features to meet specific application requirements. From sleek and compact designs for consumer electronics to rugged and weatherproof enclosures for industrial equipment, die-cast enclosure parts can be tailored to match the performance, aesthetics, and functionality of any electronic device.
Efficiency and cost-effectiveness are key considerations in electronics manufacturing, where time-to-market and production costs are critical factors in competitiveness. Die casting enables the production of enclosure parts in large volumes with minimal material waste, resulting in cost savings and streamlined production workflows. Additionally, the scalability of die casting processes allows for rapid prototyping and quick adjustments to design iterations, reducing time and costs associated with product development and manufacturing.
“The Parts We Make Today, We Ship Today”
Kinetic Die Casting Company. Inc.
6918 Beck Avenue, North Hollywood,
California 91605, United States of America
E-mail sales@kineticdc.com
USA Toll Free: (800) 524-8083 Local: (818) 982-9200
To get Prices for Die Casting Enclosures or Boxes:
Prices for Die Casting Enclosures or Boxes
Kinetic Die Casting Company makes:
Aluminum Die Casting Box Enclosure
Die Casting Aluminum Heat Sinks
Permalink: https://www.kineticdiecasting.com/kdc/empowering-electronics/
Die Castings Illuminating Brilliance
Die Casting Lighting Parts, in the world of lighting design and manufacturing, precision, durability, and aesthetic appeal are essential. Die casting, a versatile and efficient manufacturing process, plays a crucial role in producing high-quality lighting parts that meet these demanding requirements. From intricate fixtures to innovative LED components, die casting enables the creation of lighting solutions that illuminate spaces with brilliance and elegance. Let’s explore the significance of die casting in lighting parts production and its transformative impact on the industry.
Lighting fixtures are often exposed to harsh environmental conditions, including temperature fluctuations, humidity, and exposure to UV radiation. Die casting offers excellent durability and resistance to corrosion, making it an ideal manufacturing process for lighting parts designed for outdoor and industrial applications. Aluminum, zinc, and magnesium alloys commonly used in die casting provide exceptional strength and corrosion resistance, ensuring that lighting fixtures maintain their functionality and aesthetics over extended periods of use.
Aesthetic Versatility and Design Freedom. In addition to performance and durability, lighting fixtures must also meet aesthetic requirements and complement interior or exterior design schemes. Die casting offers unparalleled design freedom and versatility, allowing for the creation of lighting parts with intricate details, customized finishes, and unique shapes. From modern and minimalist designs to ornate and decorative fixtures, die-cast lighting parts can be tailored to match the style and ambiance of any environment, enhancing the overall visual appeal of spaces.
As lighting technology continues to evolve, so too does the role of die casting in shaping the future of the industry. Die casting companies invest in research and development initiatives to innovate new materials, processes, and technologies that enhance the performance, efficiency, and design flexibility of lighting parts. From lightweight alloys to advanced surface treatments and coatings, die casting enables the development of cutting-edge lighting solutions that push the boundaries of innovation and sustainability.
Die casting plays a vital role in the production of lighting parts that combine precision engineering, durability, and aesthetic appeal. From residential fixtures to commercial and industrial applications, die-cast lighting parts illuminate spaces with brilliance and elegance, enhancing both functionality and aesthetics. As lighting technology continues to evolve, die casting remains at the forefront, driving progress and innovation in the quest for more efficient, durable, and visually stunning lighting solutions.
“The Parts We Make Today, We Ship Today”
Kinetic Die Casting Company. Inc.
6918 Beck Avenue, North Hollywood,
California 91605, United States of America
E-mail sales@kineticdc.com
USA Toll Free: (800) 524-8083 Local: (818) 982-9200
To get prices for Die Casting Lighting Parts:
Quote Die Casting Lighting Part Prices
Kinetic Die Casting Company makes:
Light Fixture Die Casting Parts
Photos Die Casting Parts
Aerospace Die Casting Parts
UK Manufacturers – List of Industrial Manufacturers