Here is a listing of the 30 Die casting manufacturing companies that closed in southern California from 1994 to 2020. Alcastco Die Casting Company, Sun Valley, CA AQ Die Casting, Chatsworth, CA Arrow Die Casting Company, Los Angeles, CA ArtMold …
Continue reading
Tag Archives: #DieCastingParts
The Advantages of Aluminum Die Casting
Aluminum die casting is a widely used manufacturing process that offers numerous advantages over other casting methods. This versatile technique allows manufacturers to produce intricate and complex components with exceptional precision and cost-effectiveness. In this post, we will explore the advantages of aluminum die casting and understand why it is favored by industries worldwide.
Lightweight and Strong:
Aluminum is renowned for its excellent strength-to-weight ratio. Components produced through die casting are remarkably lightweight while maintaining high structural integrity. This advantage makes aluminum die casting ideal for applications in the automotive, aerospace, and consumer electronics industries, where weight reduction is crucial for fuel efficiency and performance.
Design Flexibility:
Die casting offers designers and engineers a high degree of freedom in component design. The process allows for the creation of complex shapes, intricate details, thin walls, and sharp angles that may be challenging to achieve with other casting methods. The versatility of aluminum die casting enables the production of aesthetically pleasing and functional components, giving manufacturers a competitive edge in the market.
Excellent Surface Finish:
Aluminum die casting results in parts with a superior surface finish. The process minimizes the need for secondary operations such as polishing or painting, reducing overall production costs. The smooth and uniform finish obtained through die casting enhances the visual appeal of the components, making them suitable for applications where appearance is crucial.
Cost-Effective:
Aluminum die casting is a cost-effective manufacturing process. High-speed production enables manufacturers to produce large quantities in a short timeframe, leading to economies of scale. The tooling costs associated with die casting can be recovered quickly due to the high productivity and efficiency of the process. Moreover, aluminum die casting machines have long service lives, further reducing production costs in the long run.
Superior Thermal Conductivity:
Aluminum possesses excellent thermal conductivity properties, making it suitable for applications where heat dissipation is critical. Components produced through aluminum die casting efficiently transfer heat, ensuring optimum performance and preventing overheating. This advantage makes it a preferred choice in industries such as automotive, LED lighting, and electronics.
Aluminum die casting offers a wide range of advantages that make it a preferred choice for manufacturers worldwide. From its lightweight and strong properties to its excellent surface finish and thermal conductivity, this manufacturing process provides unmatched design flexibility and cost-effectiveness. Ultimately, aluminum die casting helps companies produce high-quality components that meet the demands of modern industries.
“The Parts We Make Today, We Ship Today”
Kinetic Die Casting Company. Inc.
6918 Beck Avenue, North Hollywood,
California 91605, United States of America
E-mail sales@kineticdc.com
USA Toll Free: (800) 524-8083 Local: (818) 982-9200
To get prices for Die Casting Tooling Molds or Parts:
RFQ Die Casting Tooling Part Prices
Kinetic Die Casting Company makes:
Metal Casting Parts or Plastic Parts
Die Casting Tooling
Die Castings Flying High
The Crucial Role of Die Casting in Aircraft Parts Production. In the aerospace industry, the choice of manufacturing processes is crucial in ensuring the performance and integrity of aircraft components. Die casting emerges as a cornerstone technology, offering unparalleled precision, efficiency, and quality in the production of critical aircraft parts. From engine components to structural elements, die casting plays a pivotal role in shaping the future of aviation, driving innovation and excellence in aircraft manufacturing. Let’s explore the significance of die casting in aircraft parts production and its transformative impact on the aerospace industry.
Die casting plays a vital role in the production of aircraft parts that combine precision engineering, durability, and safety in the aerospace industry. From engine components to structural elements, die-cast aircraft parts empower aviation with reliability, performance, and efficiency, shaping the future of flight. As aerospace technology continues to advance, die casting remains at the forefront, driving progress and innovation in the quest for safer, more efficient, and more sustainable aircraft solutions.
Efficiency and cost-effectiveness are critical considerations in aircraft manufacturing, where time-to-market and production costs are key factors in competitiveness. Die casting enables the production of aircraft parts in large volumes with minimal material waste, resulting in cost savings and streamlined production workflows. Additionally, the scalability of die casting processes allows for rapid prototyping and quick adjustments to design iterations, reducing time and costs associated with product development and manufacturing.
Aircraft parts demand the highest levels of precision and quality to ensure the safety and performance of flight operations. Die casting enables the production of aircraft parts with intricate geometries, tight tolerances, and complex features that are essential for meeting the rigorous standards of the aerospace industry. Whether it’s engine housings, wing components, or landing gear parts, die-cast aircraft parts provide the structural integrity and precision engineering necessary for safe and reliable operation in demanding flight conditions.
Aircraft operate in a wide range of environmental conditions, from extreme temperatures and high altitudes to dynamic forces and aerodynamic
As aerospace technology continues to evolve, so too does the role of die casting in shaping the future of aviation. Die casting companies invest in research and development initiatives to innovate new materials, processes, and technologies that enhance the performance, efficiency, and safety of aircraft parts. From lightweight alloys to advanced surface treatments and coatings, die casting enables the development of cutting-edge aircraft solutions that push the boundaries of innovation and sustainability.
Aircraft parts must adhere to stringent quality standards and regulatory requirements to ensure airworthiness and compliance with aviation regulations. Die casting companies specializing in aircraft parts production undergo rigorous certification processes to demonstrate compliance with industry-specific standards such as AS9100 and NADCAP. These certifications provide assurance that die-cast aircraft parts meet the highest standards of quality, reliability, and performance, instilling confidence in aerospace manufacturers, airlines, and regulatory authorities.
“The Parts We Make Today, We Ship Today”
Kinetic Die Casting Company. Inc.
6918 Beck Avenue, North Hollywood,
California 91605, United States of America
E-mail sales@kineticdc.com
USA Toll Free: (800) 524-8083 Local: (818) 982-9200
Get prices for Die Casting Tooling Molds or Parts:
Quote Die Casting Airplane Part Prices
Kinetic Die Casting Company makes:
Airplane Die Casting Parts
Light Fixture Die Casting Parts
Manufacturing Companies – Business Directory UK – Details of UK Industrial Manufacturers and Suppliers.
Web Design Directory – A list of website designers in Northern Ireland.
Die Casting Fortifying Defense
The Vital Role of Die Casting in Military Parts Production and Manufacturing Paramount Importance. From mission-critical components to rugged equipment, every part must meet stringent standards to ensure the safety and effectiveness of military operations. In this landscape, die casting emerges as a cornerstone technology, enabling the production of high-quality military parts with unmatched precision and efficiency. Let’s explore the significance of die casting in military parts production and its crucial role in bolstering national defense.
Military operations rely on a vast array of specialized components, ranging from aircraft and vehicle parts to weapon systems and communication devices. Die casting plays a crucial role in manufacturing these mission-critical components, providing the precision and durability required for demanding military applications. Whether it’s lightweight aircraft components, rugged vehicle chassis, or intricate weapon parts, die casting ensures that military equipment meets the rigorous standards of performance, reliability, and safety.
Precision is paramount in military operations, where accuracy and reliability can mean the difference between success and failure. Die casting enables the production of military parts with intricate geometries, tight tolerances, and complex features, ensuring optimal performance and functionality. From precision-machined weapon components to intricately designed avionics housings, die-cast military parts deliver the precision engineering required for critical missions and operations.
In military environments, equipment must withstand extreme conditions, including high temperatures, heavy loads, and harsh environments. Die casting offers exceptional strength and durability, making it an ideal manufacturing process for military parts subjected to rigorous operational demands. Aluminum, zinc, and magnesium alloys commonly used in die casting provide excellent mechanical properties, corrosion resistance, and thermal conductivity, ensuring that military equipment remains robust and reliable in the face of adversity.
Efficiency and cost-effectiveness are key considerations in military procurement, where budgets must be optimized without compromising on quality or performance. Die casting offers a cost-effective solution for producing high-quality military parts in large volumes. By utilizing reusable molds, automated production processes, and efficient material usage, die casting minimizes manufacturing costs while ensuring consistent quality and reliability. This cost-effectiveness enables military organizations to procure the parts they need to support their missions while maximizing the value of their budgets.
Military parts must adhere to stringent standards and regulations to ensure compatibility, interoperability, and safety. Die casting companies specializing in military parts production undergo rigorous certification processes to demonstrate compliance with industry-specific requirements, such as MIL-STD, AS9100, and ITAR regulations. These certifications provide assurance that die-cast military parts meet the highest standards of quality, reliability, and performance, instilling confidence in military organizations and end-users alike. As military technology evolves, so too does the role of die casting in meeting the evolving needs of defense applications. Die casting companies invest in research and development initiatives to innovate new materials, processes, and technologies that enhance the performance and capabilities of military parts. From lightweight armor materials to advanced sensor housings, die casting continues to drive innovation in defense manufacturing, ensuring that military equipment remains at the forefront of technological advancement.
“The Parts We Make Today, We Ship Today”
Kinetic Die Casting Company. Inc.
6918 Beck Avenue, North Hollywood,
California 91605, United States of America
E-mail sales@kineticdc.com
USA Toll Free: (800) 524-8083 Local: (818) 982-9200
To get prices for Die Casting Military Parts:
Quote Die Casting Military Parts
Kinetic Die Casting Company makes:
American Die Casting Company
Military Die Casting Parts
Die Casting Tooling
Permalink: https://www.kineticdiecasting.com/kdc/die-casting-fortifying-defense/
Taking Flight with Precision Die Casting
Aerospace engineering places a premium on lightweight solutions without compromising strength and durability. Die casting, with its ability to produce complex shapes and intricate features using lightweight alloys such as aluminum and magnesium, offers an ideal solution for manufacturing airplane parts. By leveraging die casting techniques, engineers can design and fabricate components that reduce overall aircraft weight, leading to improved fuel efficiency, increased payload capacity, and enhanced performance. The heart of any aircraft, the engine relies on a multitude of precision-engineered components to generate thrust efficiently and reliably. From turbine blades and compressor housings to engine mounts and heat exchangers, die casting plays a vital role in the production of these critical parts. By harnessing the precision and repeatability of die casting processes, aerospace manufacturers can produce engine components that meet the exacting standards of performance, reliability, and safety demanded by the industry. Aerospace structures must withstand immense forces and stresses during flight, requiring components of exceptional structural integrity and reliability. Die casting enables the production of parts with uniform grain structure and minimal porosity, resulting in enhanced mechanical properties and fatigue resistance. Whether it’s fuselage components, wing brackets, or landing gear assemblies, die-cast parts contribute to the overall strength and durability of aircraft structures, ensuring the safety and longevity of flights.
When precision and reliability are paramount, die casting offers a versatile solution for producing intricate housings, enclosures, and heat sinks. These components provide crucial protection and thermal management for sensitive electronic systems onboard aircraft, ensuring optimal performance and longevity in demanding aerospace environments. By leveraging die casting techniques, manufacturers can achieve the tight tolerances and intricate geometries required for advanced avionics applications. As aerospace technology continues to evolve, so too does the role of die casting in shaping the future of flight. Manufacturers and engineers collaborate to push the boundaries of innovation, leveraging advanced materials, design optimization techniques, and cutting-edge manufacturing processes to meet the evolving needs of the aerospace industry. From additive manufacturing and simulation-driven design to digital twin technology and integrated supply chain solutions, the aerospace die casting sector remains at the forefront of innovation, driving progress and shaping the next generation of aircraft systems and components.
“The Parts We Make Today, We Ship Today”
Kinetic Die Casting Company. Inc.
6918 Beck Avenue, North Hollywood,
California 91605, United States of America
E-mail sales@kineticdc.com
USA Toll Free: (800) 524-8083 Local: (818) 982-9200
Get prices for Die Casting Tooling Molds or Parts:
Quote Die Casting Aerospace Part Prices
Kinetic Die Casting Company makes:
Aerospace Die Casting Parts
Light Fixture Die Casting Parts
Zinc Die Cast Knobs
Zinc die-cast knobs are essential components in various industries, offering durability, versatility, and aesthetic appeal. With excellent strength and corrosion resistance properties, zinc die-cast knobs have become a popular choice for manufacturers due to their ability to withstand both indoor and outdoor applications. This article will delve deeper into the characteristics, benefits, applications, and considerations of zinc die-cast knobs in the manufacturing sector.
Zinc die-cast knobs are manufactured through a process called die casting, which involves injecting molten zinc into a steel mold cavity under high pressure. This process allows for the production of intricate and precise designs, making zinc die-cast knobs a versatile option for various applications. The use of zinc as a base material also contributes to the knobs’ strength and resistance to wear and tear, ensuring a long lifespan even in demanding environments.
One of the key advantages of zinc die-cast knobs is their aesthetic appeal. The material can be easily plated or coated with various finishes, including chrome, nickel, or powder coating, to match different design requirements. This versatility in finishing options allows manufacturers to tailor the appearance of zinc die-cast knobs to suit a wide range of products, from industrial machinery to consumer electronics.
In addition to their visual appeal, zinc die-cast knobs offer excellent tactile feedback and ergonomic functionality. The knobs can be designed with different shapes, sizes, and textures to provide users with a comfortable grip and precise control. This makes zinc die-cast knobs ideal for applications where precise adjustment or manipulation is required, such as in instrumentation panels, control systems, or consumer appliances.
Another significant benefit of zinc die-cast knobs is their cost-effectiveness. The die-casting process allows for high production volumes at a relatively low cost per unit, making zinc die-cast knobs a cost-efficient solution for manufacturers looking to scale up their production. Furthermore, the durability and longevity of zinc die-cast knobs reduce maintenance and replacement costs, providing long-term value for businesses.
Zinc die-cast knobs find wide applications across various industries, including automotive, electronics, furniture, and machinery. In the automotive sector, zinc die-cast knobs are used in dashboard controls, door handles, and HVAC systems, providing drivers with reliable and durable components. In the electronics industry, zinc die-cast knobs are commonly found in audio equipment, home appliances, and industrial machinery, where precision and durability are paramount. When considering zinc die-cast knobs for a specific application, manufacturers should take into account factors such as operating environment, load requirements, and aesthetic considerations. It is essential to work closely with experienced design engineers and material specialists to ensure that the chosen zinc die-cast knobs meet the desired performance criteria and quality standards.
“The Parts We Make Today, We Ship Today”
Kinetic Die Casting Company. Inc.
6918 Beck Avenue, North Hollywood,
California 91605, United States of America
E-mail sales@kineticdc.com
USA Toll Free: (800) 524-8083 Local: (818) 982-9200
To get prices for Die Casting Tooling Molds or Parts:
RFQ Die Casting Tooling Part Prices
Kinetic Die Casting Company makes:
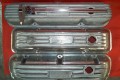
Die Casting Bracket Hardware
Airplane Die Casting Parts
Permalink: https://www.kineticdiecasting.com/kdc/zinc-die-cast-knobs/